In-service Lube Oil Sampling, Pt. 2 !
Oil sample locations and improved sampling equipment
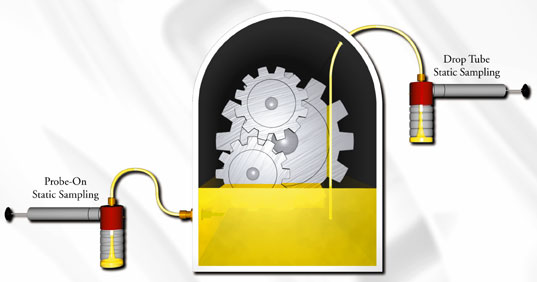
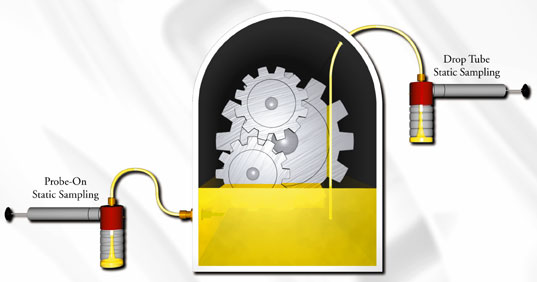
Selecting the best location for a sample
“Maximize the data density” of a sample by ensuring we collect the sample with the best procedure and at the optimal location. For example, taking the sample downstream of the filter would result in missing critical wear or contaminant particles that would have been removed from by the filter. Samples should be taken upstream of filters and downstream of machinery components.
Collecting samples of oil that is circulating
In any circulating system we want to collect a lubricant sample in turbulent flow and downstream of critical lubricated equipment. This ensures that the sample is well mixed and has the best chance of capturing wear debris from the critical lubricated components of the system.
Collecting a sample from oil that is stagnant or flowing in a straight line (laminar) is not as representative as turbulent flow. Laminar flow refers to parallel fluid layers adjacent to each other without mixing. Wear or contaminant particles flow along with the fluid. If we take a sample under these conditions, some of the particles will “fly-by” our sampling point. We will miss important information about the particles that are circulating in the system. We should take samples at locations where there is turbulent flow when possible. Piping elbows are perfect turbulent flow locations. Mixing of the layers occurs at these points.
The best place to take samples is at an elbow on a return line, downstream of machine components but upstream of filters. In a reservoir the fluid will rest and can lose concentration of any wear metal debris. Although the second-best sampling location is on the supply side of a circulating system, the oil flows through a filter is still before the oil flows through a filter. Much of any active wear debris will remain suspended in the oil even as it rests for the minutes that it would circulate through a reservoir before being pumped back through the system.
Collecting samples of oil that is NOT circulating
Oil reservoir, gearbox sump, or from any drain location is where oil is considered non-circulating. Since these locations may not be capturing oil in turbulent flow, they can miss out on capturing fresh wear material from lubricated components. When faced with having to sample non-circulating oil we can still capture the best samples available.
Drain Port Sampling: Particles and water will settle to the bottom of the sump, resulting in a bad (non-representative) sample. Drain off and discard a sufficient volume of oil before taking the sample to be sent to your laboratory for used oil analysis. This will remove as much stagnant debris and water from the sample which does not represent the oil that’s actively lubricating critical components. A preferable way to take a drain sample is to use a pitot tube, which extends into the fluid so that the sample will be more representative. The tube should drop down to the midpoint depth of the fluid level in the reservoir.
Handheld Vacuum Pump and Tubing: Collect a sample from the fill port of a reservoir or gearbox sump with a handheld vacuum pump and polyethylene tubing. This technique allows the technician to collect oil that is not resting near a drain, therefore it’s an improvement from a drain sample.
This method has several drawbacks. Inserting the tube to the correct depth of reservoir oil and using a consistent technique can be difficult. Soft tubing will bend and curl up at the fluid line and it can be difficult to get the right angle of the tubing to enter the fluid. Fill port screens may also be time consuming to remove to prepare for collection. Lastly, the tip of the tubing can scrape metal surfaces and contaminate the sample.
Installing the right equipment to facilitate sampling
Hydraulic Oil Adapter Kit
Image from Trico Corporation.
Minimess Oil Sampling Port: A minimess oil sampling port is a type of sampling valve that is commonly used for taking oil samples from hydraulic and lubrication systems. It is a compact, self-sealing valve that can be installed directly into the system for easy and convenient collection. Here are some of the advantages and disadvantages of using a minimess oil sampling port:
Advantages of a minimess port:
1. Easy to install: Minimess oil sampling ports are designed to be easy to install, with a threaded body that can be screwed directly into the system.
2. Easy to use: The self-sealing valve design of the minimess port makes it easy to take oil samples quickly and cleanly.
3. Minimal system downtime: Because the minimess port can be installed without draining the system, there is minimal downtime required for installation.
4. Clean: The minimess port helps prevent contamination of the oil sample, as it is designed to seal tightly when not in use.
5. Compatible with different types of oil: Minimess ports can be used with a variety of different types of oils and fluids, making them a versatile choice for oil sampling.
Disadvantages of a minimess port:
1. Cost: Minimess oil sampling ports can be more expensive than other types of sampling valves, which may be a consideration for some applications.
2. Maintenance: Like any type of valve or sampling device, minimess ports require regular maintenance to ensure proper operation and prevent leaks.
3. Limited flow rate: The flow rate through a minimess port is limited, which may be a consideration for larger hydraulic or lubrication systems.
4. Limited pressure rating: Minimess ports typically have a limited pressure rating, which may make them unsuitable for use in high-pressure systems.
Overall, minimess oil sampling ports are a convenient and reliable option for taking oil samples from hydraulic and lubrication systems. They are easy to install and use and help prevent contamination of the oil sample. However, their higher cost and limitations in flow rate and pressure rating may be a consideration for some applications.
Additional alternative – the Portable Filter Cart: Portable filter carts will typically have at least one oil sample location on them. Filter carts can be equipped with a bypass valve so that oil can be circulated without flowing through the filters. Circulating the oil for a few minutes allows us to take a representative oil sample. After the sample is taken, switch the valve to filter the oil. This method lets you take a representative before and after any external filtration work.
Sample Methods Summary
Accurate analysis and diagnosis of an oil system depend on obtaining a representative sample, free from contaminants. Regardless of the sampling method used, it is crucial to follow proper procedures and guidelines to ensure the sample collected accurately reflects the oil's condition.
To ensure that the oil sample is representative, the sampling location should be flushed before collecting the sample. Clean and properly labeled sample containers should be used to avoid contamination. It is also essential to prevent any contact between the sample and surfaces or materials that may introduce contaminants.
Consistency in sampling is crucial to accurately assess the oil system's condition over time. The best way to ensure consistent sampling is to have a written procedure that outlines the steps to be followed, including the frequency of sampling, the type of container to be used, and any flushing or cleaning procedures necessary.
When developing a sampling procedure, consider the specific needs of your oil system, the equipment to be used, and the type of analysis required. Consult industry standards and guidelines and involve key stakeholders in the process. It is also essential to review and update the procedure regularly to ensure it remains current and effective.
Sending the Sample to the Laboratory
When submitting a used oil sample for analysis, it is important to provide certain information to ensure that the laboratory can perform an accurate and meaningful analysis. This information includes equipment information, sampling date, service hours/mileage, operating conditions, and any additional relevant information such as recent maintenance, repairs or any unusual observations. These observations may be unusual equipment noise, vibration, or operating temperature. By providing this information, the laboratory can better determine the condition of the oil and machine to make more accurate recommendations for maintenance and equipment performance. Sometimes you may not have all of the above information so just include as much information as possible.
Conclusion of the Blog Information
Overall, oil sampling is an essential tool for maintaining the reliability and performance of machinery and equipment. By using appropriate sampling methods and following proper procedures, maintenance professionals can ensure that oil samples are accurate, representative, and useful for making informed maintenance decisions. Good sampling technique will go a long way to improving your reliability program and reducing unexpected downtime and lost revenue.
At MRT Laboratories, we are here to help optimize sample collection and quality. Whether you need guidance on sampling technique or have questions about our services, our team of STLE/ICML certified professionals is always available to assist you. Please don't hesitate to reach out to us. We value your input and are committed to providing the highest level of support and expertise. You can email us at info@mrtlaboratories.com or call us at 713-944-8381