Benefitting from Full-Film Hydrodynamic Lubrication
Continuation of Lubrication Regimes - Hydrodynamic
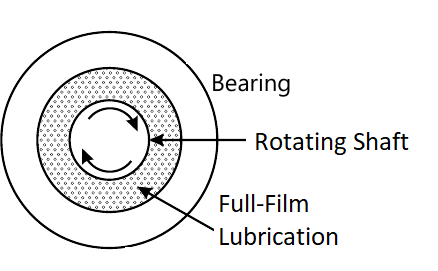
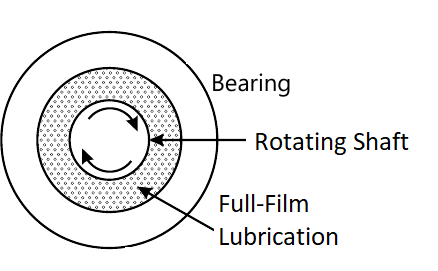
Full-Film, Hydrodynamic Lubrication
A hydrodynamic lubrication regime occurs when a full fluid film is formed between two surfaces in relative motion, effectively separating them and reducing friction and wear. In this regime, the lubricant's primary function is to create and maintain a pressurized fluid film that supports the load and prevents direct contact between the surfaces.
Characteristics of Hydrodynamic Lubrication:
1. Fluid film formation: Hydrodynamic lubrication relies on the formation of a thick fluid film between the surfaces, which provides complete separation and minimizes contact.
2. Pressure generation: As the surfaces move relative to each other, the lubricant gets squeezed between them, generating pressure that supports the load and maintains the fluid film.
3. High-speed operation: Hydrodynamic lubrication is particularly effective at higher speeds where the relative motion of the surfaces generates sufficient hydrodynamic pressure to sustain the fluid film.
Mechanisms of Hydrodynamic Lubrication:
1. A wedge effect: The converging shape of the lubricant film due to the surfaces' geometry creates a wedge-like action, generating pressure and lifting the load, effectively separating the surfaces.
2. Fluid shear: The relative motion between the surfaces causes shear forces within the lubricant, creating a hydrodynamic pressure that further supports the load and maintains the fluid film.
Factors Influencing Hydrodynamic Lubrication:
1. Operating conditions: Hydrodynamic lubrication is more pronounced at higher speeds and loads where the hydrodynamic pressure generated is sufficient to sustain the fluid film.
2. Viscosity: The viscosity of the lubricant is crucial in hydrodynamic lubrication, as it affects the film thickness and the ability to generate and maintain the necessary fluid pressure.
3. Surface geometry: The shape and design of the surfaces, including clearances and surface roughness, influence the fluid film formation and the hydrodynamic pressure developed.
The stages to create full film, hydrodynamic lubrication:
1. Initial contact: Initially, the surfaces are in contact and the lubricant is squeezed out from the clearance between them.
2. Inlet zone: As the surfaces continue to move, the lubricant enters the inlet zone, where the fluid film starts forming.
3. Full film zone: Further into the motion, the fluid film thickness increases, reaching its maximum in the full film zone, fully separating the surfaces.
Hydrodynamic lubrication is commonly employed in journal bearings used in engines, turbines, and other rotating machinery to minimize friction and support heavy loads. It’s also ideal for sliding surfaces, such as sliding guides, machine tool slides, and hydraulic cylinders, which benefit from hydrodynamic lubrication to reduce wear and friction.
Hydrodynamic lubrication offers several advantages:
1. Excellent load-bearing capacity: The thick fluid film generated in hydrodynamic lubrication can support high loads and reduce friction effectively.
2. Lower friction and wear: Hydrodynamic lubrication minimizes direct contact between the surfaces, resulting in reduced friction and wear.
However, hydrodynamic lubrication also has limitations:
1. Dependence on speed: Hydrodynamic lubrication is more effective at higher speeds where sufficient hydrodynamic pressure can be generated. At low speeds, the fluid film may be less developed, leading to increased contact and higher friction.
2. Start-up and shutdown: Hydrodynamic lubrication may take time to establish at start-up and may not be fully effective during shutdown, which can lead to increased wear during these transient operating conditions.
To compensate for the lack of full film lubrication at start up, a hydrostatic lift is used. Hydrostatic lift offers a vital solution for addressing start-up and transient challenges. This mechanism involves pressurized fluids that create a fluid cushion between surfaces, preventing direct contact and reducing wear. During start-up, when immediate hydrodynamic lubrication can be difficult, hydrostatic lift proves its effectiveness. By introducing pressurized fluid externally, a thin fluid film rapidly forms even at low speeds, preventing initial friction and wear.
External pumps and compressors will deliver fluid through dedicated channels in bearing surfaces. Turbines and centrifugal compressors commonly require hydrostatic lift since they commonly experience frequent start-stop cycles. A properly maintained hydrostatic lift system will significantly extend machinery lifespan.
Understanding hydrodynamic lubrication is crucial for selecting appropriate lubricants, optimizing clearances and surface design, and operating machinery at optimal speeds and loads. In the next section, we will explore elastohydrodynamic lubrication (EHL), which combines aspects of hydrodynamic lubrication with elastic deformation of the surfaces.