Final Lubrication Regime: Elasto-Hydrodynamic Lubrication
Understanding Full-Film, Elasto-hydrodynamic Lubrication
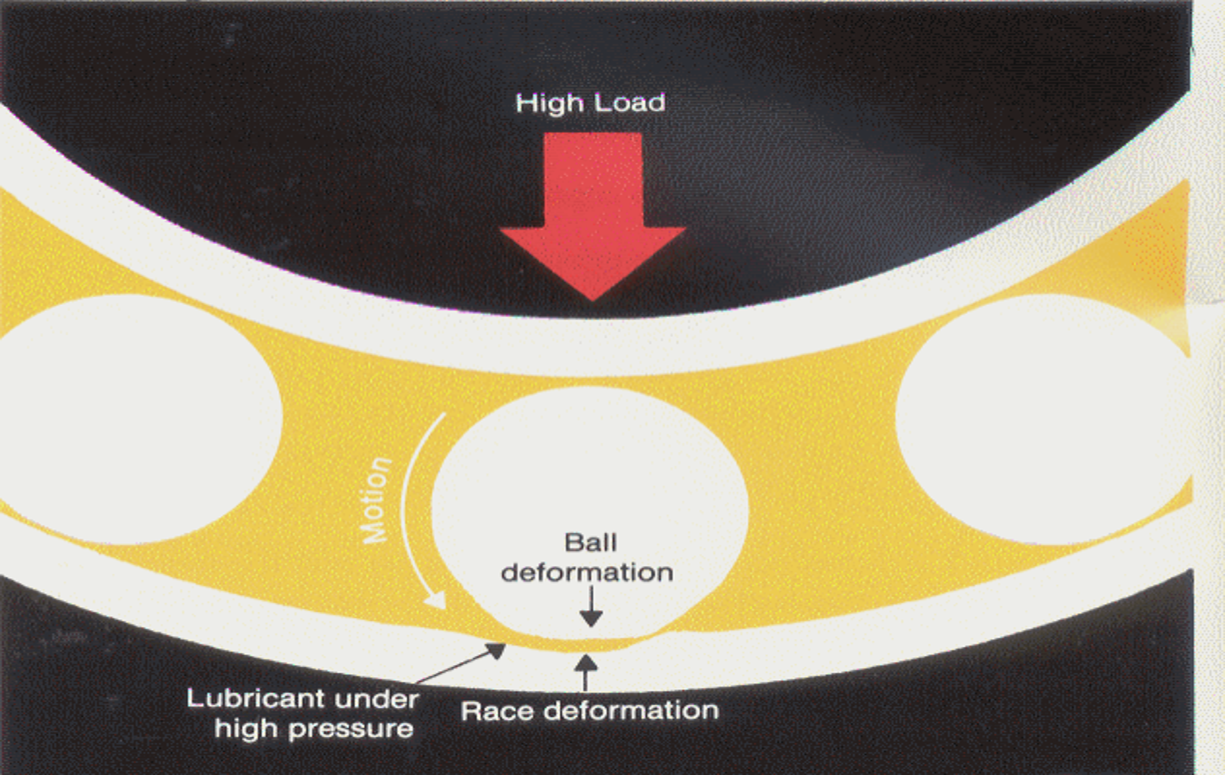
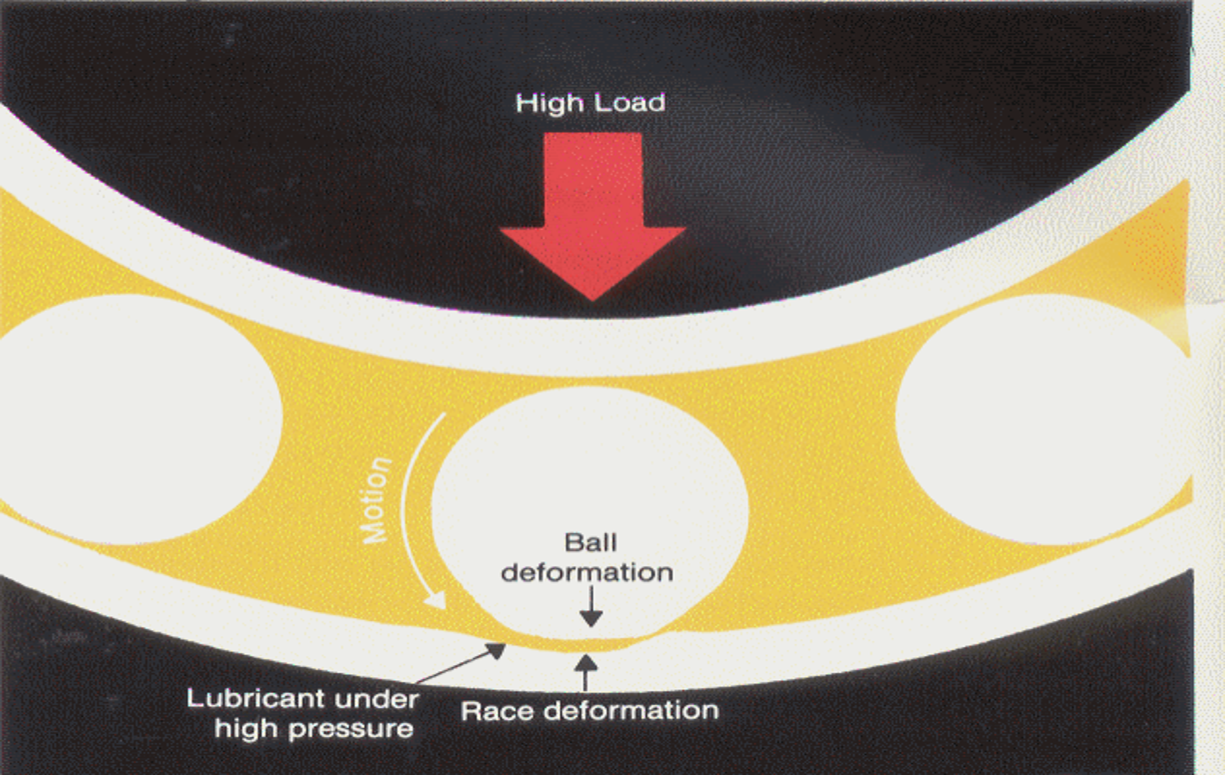
Elasto-hydrodynamic lubrication (EHL) is a specialized lubrication regime that combines hydrodynamic lubrication principles with the elastic deformation of contacting surfaces. It is utilized in applications with high loads, high speeds, and tight clearances, requiring a lubricant capable of withstanding extreme operating conditions.
Key characteristics of elasto-hydrodynamic lubrication include the elastic deformation of surfaces under the pressure generated by the lubricant film, high contact pressures leading to localized elevated temperatures within the film, and the viscoelastic behavior of the lubricant, exhibiting both viscous and elastic properties. In the contact zone the pressure on the lubricant film layer causes the lubricant viscosity to increase significantly where it can be almost solid, which causes elastic surface deformation of the lubricated surface. Elastic deformation, by definition, indicates that the microscopic change in shape in the contact zone is temporary and the lubricated component resumes is original shape once pressure is reduced.
Is elastic deformation of the surface a good thing? Yes, it is. Elasto-hydrodynamic lubrication operates through several mechanisms to reduce friction and wear. The deformation and load support mechanism involves elastic deformation of surfaces as the lubricant film thickness decreases, resulting in a larger contact area and increased load-carrying capacity. Shear-thinning and film generation occur as the lubricant experiences decreased viscosity under high shear rates, allowing for the formation of a thinner yet robust lubricating film. The elastic deformation of surfaces dissipates energy, reducing frictional losses and heat generation.
Several factors influence the effectiveness of elasto-hydrodynamic lubrication. Higher loads and pressures promote greater deformation of surfaces, enhancing load support. Surface roughness and finish affect the contact area and the lubricant's ability to form and maintain an effective elasto-hydrodynamic film. The viscosity and additives of the lubricant play a crucial role in film formation and stability, particularly under extreme operating conditions.
In elasto-hydrodynamic lubrication, the lubricant film formation and deformation progress through stages, starting with initial contact and deformation as the surfaces come into contact and creating a larger contact area. This process leads to full-film formation, where the lubricant film reaches its maximum thickness and separates the surfaces completely as they continue to move.
Elasto-hydrodynamic lubrication finds applications in various high-load and high-speed systems, including automotive engines (e.g., camshafts, crankshafts, and connecting rods) and rolling element bearings (e.g., ball and roller bearings).
Advantages of elasto-hydrodynamic lubrication include its high load-carrying capacity due to surface elastic deformation and its ability to minimize friction and wear compared to other lubrication regimes. However, it is sensitive to surface finish, lubricant properties, and critical operating conditions, requiring appropriate lubricant film thickness and specific load and speed ranges to be effective.
Understanding elasto-hydrodynamic lubrication is crucial for selecting lubricants with suitable viscosity and additives, optimizing surface finishes, and designing systems capable of withstanding high loads and speeds.