Challenges of Properly Formulating a Lubricant with Additives
Blending Procedure and Compatibility are Critical to Successful Additization
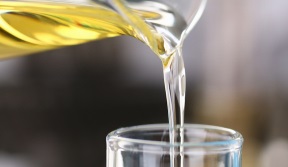
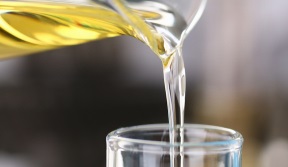
Many MRT customers are the operators of multi-million-dollar mechanical equipment that runs without interruption for months or even years. We also assist certain lubricant manufactures that will ask us to test new formulations throughout the process of adding and blending additives into their base oils.
Formulating lubricants with additives is a complex process that requires careful consideration of a number of factors, including the type of base oil, the operating conditions of the lubricant, and the specific challenges that need to be addressed.
Here are some specific examples of challenges that formulators face when working with additives:
· Balancing multiple additive functions: Formulators need to balance the performance of different additives to ensure that the lubricant meets the needs of the specific application. For example, a lubricant for a high-temperature application may need to contain additives that reduce friction and protect against wear at elevated temperatures. However, these additives may interact with each other in a way that reduces their performance. Formulators need to carefully select and balance different additives to ensure that they work together effectively to meet the needs of the application.
· Compatibility with other additives and base oils: Formulators need to ensure that the additives they select are compatible with each other and with the base oil. If additives are not compatible, they can interact with each other or with the base oil in a way that reduces their performance or even causes problems, such as sludge formation.
· Environmental and regulatory considerations: Many countries and regions have regulations that restrict the use of certain additives. Additionally, formulators need to be aware of the environmental impact of the additives they use. For example, some additives may be toxic or persistent in the environment. Formulators need to select additives that are environmentally friendly and compliant with all applicable regulations.
ZDDP and detergents can interact with each other in a way that reduces their performance. Detergents can remove the ZDDP layer from metal surfaces, which can reduce the anti-wear protection of the lubricant. This interaction can be particularly problematic in high-temperature applications, where the ZDDP layer is more likely to be removed by detergents. Formulators can overcome this challenge by selecting detergents that are less likely to interact with ZDDP. Additionally, they can increase the amount of ZDDP in the lubricant to compensate for the loss of anti-wear protection.
Another approach is to use a different type of anti-wear additive, such as a molybdenum disulfide (MoS2) additive. MoS2 additives are not as susceptible to interaction with detergents as ZDDP additives. Overall, the interaction of ZDDP and detergents is an important consideration for formulators when developing lubricants. By carefully selecting and balancing different additives, formulators can create lubricants that provide excellent performance, protection, and durability.