Decoding the Mystery: When ICP and FDM Readings Don't Align
How to compare Iron from ICP and FDM Instruments in Used Oil Analysis
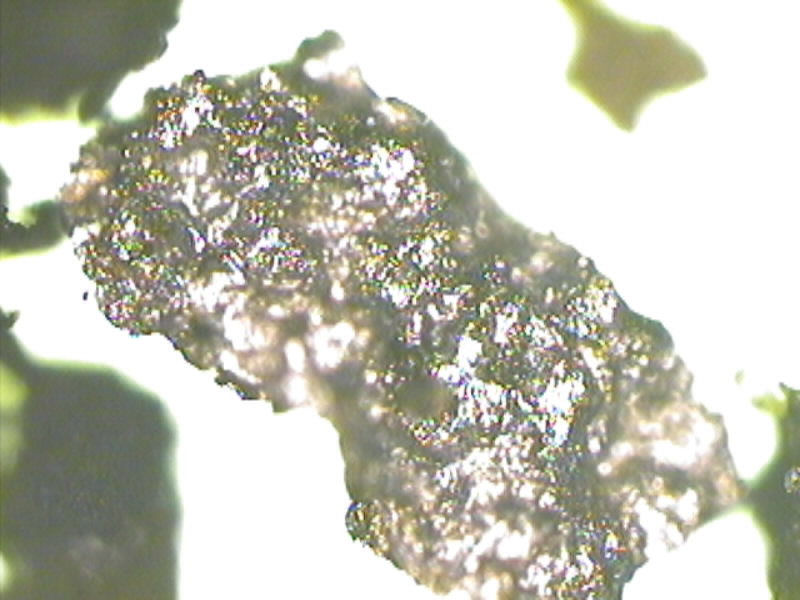
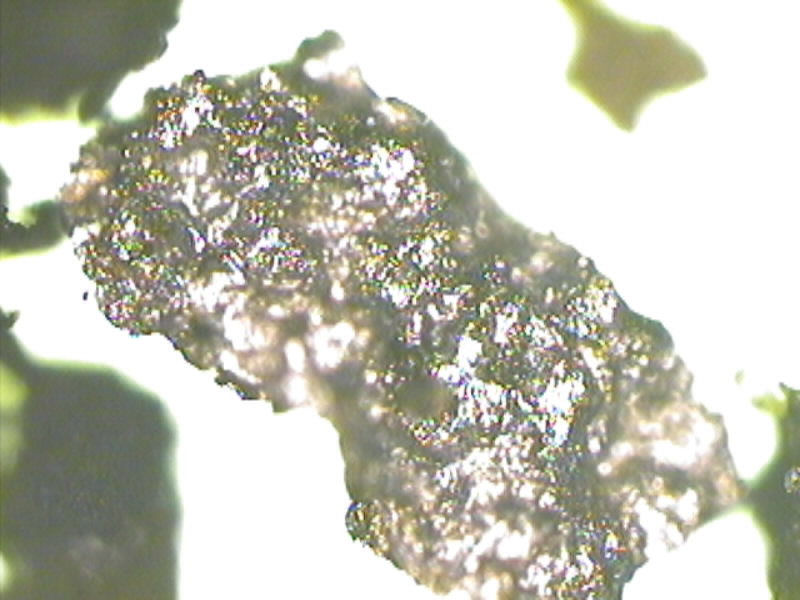
Used oil analysis is a powerful tool for keeping your equipment running smoothly and avoiding costly breakdowns. But what happens when the results you get seem contradictory? This can be especially puzzling when readings from different analysis methods, like ICP (Inductively Coupled Plasma) and FDM (Ferrous Density Meter), tell different stories.
The Case of the Curious Iron:
Let us imagine a scenario where your oil analysis shows a low iron value in parts per million by ICP but a high iron reading in parts per million by FDM. This might seem like a contradiction, but it is not uncommon, and it can actually reveal valuable insights into your equipment's health.
Understanding the Discrepancy:
Here are why these readings might differ:
• ICP: This method measures the total elemental iron present in the oil. ICP detects magnetic and nonmagnetic iron oxides (rust) and has a size limitation of about 5 microns. In other words, the instrument can detected total iron in a sample in parts per million for particles that are great than or equal to 5 microns in size
• FDM (ferrous density meter): FDM works by using a magnetic field. This device directly detects ferrous wear debris that is magnetic. FDM does not have the same size limitation as ICP. The debris that this instrument can detect must be magnetic. For example, much of rust is not magnetic. Tin, also a common wear metal that is found in oil samples, is not magnetic so an FDM will not detect that metal.
What Does It Mean if the ICP and the FDM generate materially different results for iron in ppm in an oil sample? How is that information useful?
This discrepancy in test results for iron in ppm can point to several possibilities:
• Specific wear mechanisms: The high FDM reading could indicate wear concentrated on components like gears or bearings, releasing larger ferrous debris. Meanwhile, the low ICP iron might suggest wear of other components generating smaller, non-ferrous particles.
• Iron oxide formation: If iron is present as oxides, the particles will be detected by ICP. However, the FDM directly detects magnetic ferrous particles, potentially explaining the higher reading.
• Measurement limitations: Both methods have their limitations, and factors like oil viscosity or particle size distribution can influence the readings.
Going Deeper: The Power of the Full Ferrogram
To unravel the mystery behind these discrepancies, a full analytical ferrogram can be your next step. A Ferrogram, or ferrographic analysis, determines the concentration, general size ranges, shape, and several of the metal types of wear particles through microscopic examination with the goal of heading off the accelerated wear that tends to precede equipment failure. This visual analysis of microscopic particles in an oil sample provides invaluable insights:
• Particle size and morphology: It reveals the size and shape of iron particles, helping differentiate between normal wear debris and abnormal wear modes.
• Composition analysis: It identifies the specific elements present in the particles, pinpointing potential contamination sources.
• Wear trend monitoring: Comparing ferrograms over time can track the progression of wear and identify early signs of trouble.
When to Consider a Ferrographic Analysis (Ferrogram):
A ferrogram is especially beneficial when:
• You have unexplained high iron readings by FDM (ferrous debris density test).
• You are dealing with critical equipment where early wear detection is crucial.
• You are experiencing unusual performance changes or noise vibrations.
• You want to establish a baseline for wear monitoring.
Do not Let Contradictions Confuse You:
Remember, contradictory readings in oil analysis are often opportunities for deeper understanding. By combining different methods like ICP and FDM, and leveraging the power of a full analytical ferrogram, you can gain comprehensive insights into your equipment's health and make informed maintenance decisions.
Contact us today at MRT Laboratories to discuss your specific needs and how our advanced oil analysis services can help you optimize equipment performance and prevent costly breakdowns.