Integrating Vibration and Oil Analysis
Implementing an Enhanced Reliability Program with Vibration and Oil Analysis
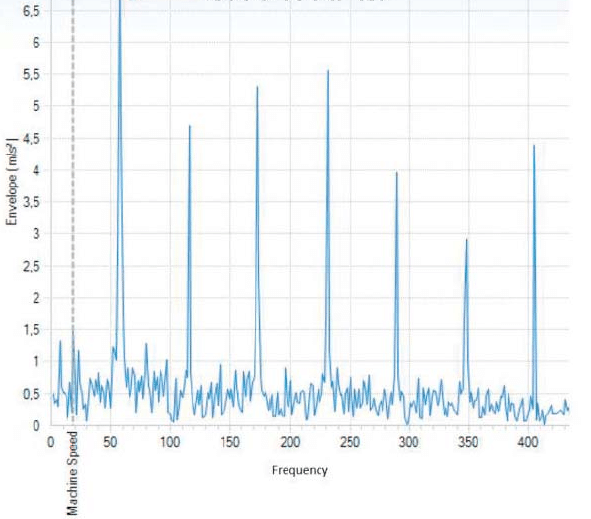
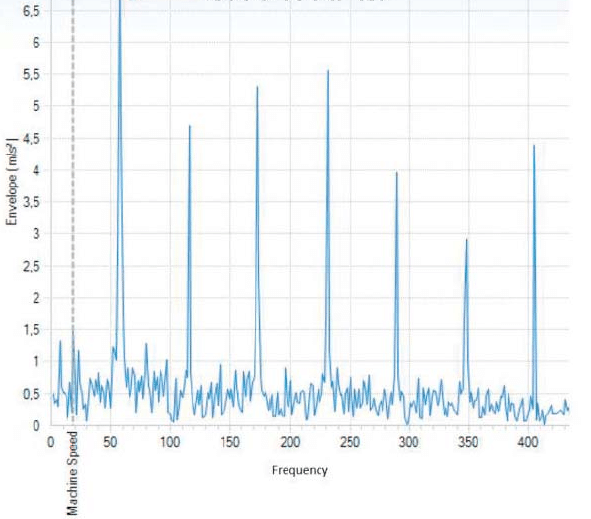
While both vibration analysis and used oil analysis play integral roles in predictive maintenance, each method offers distinct advantages and capabilities.
Vibration analysis excels in identifying mechanical and operational issues associated with rotating machinery, such as misalignment, unbalance, and bearing faults. Its nonintrusive nature allows for real-time monitoring and early detection of potential problems, enabling timely maintenance interventions to prevent costly downtime.
On the other hand, used oil analysis offers unique insights into wear, contamination, and the overall condition of lubrication systems. By analyzing the physical and chemical properties of lubricating oil, used oil analysis can detect subtle changes indicative of impending issues, providing an early warning system for potential failures. The table below summarizes the strengths and weaknesses of each one.
When combined, these two methods provide a comprehensive approach to equipment health monitoring. Vibration analysis primarily focuses on the mechanical aspects of machinery, while used oil analysis provides insights into lubrication system health and internal component wear. By integrating these techniques, organizations can leverage the strengths of each method to enhance predictive maintenance efforts, minimize downtime, and optimize equipment reliability.
Implementing an Enhanced Reliability Program
Adopting an integrated approach to reliability that combines both vibration analysis and used oil analysis can significantly enhance the predictive maintenance strategies of any organization. Here are key steps to effectively implement an enhanced reliability program:
1. Assessment of Current Practices
Start by conducting a thorough assessment of your existing maintenance and reliability practices. Identify what methods are currently in use, the frequency of these activities, and their effectiveness. This review should also include interviews with maintenance personnel to understand their experiences and insights, which can reveal hidden challenges or opportunities for improvement.
2. Training and Skill Development
Ensure that your maintenance team is professionally trained in both vibration analysis and used oil analysis. This might involve sending staff to specialized training courses, inviting experts to conduct workshops, or subscribing to online courses. It is crucial that the team not only understands how to perform the analyses but also how to interpret the data and make informed decisions.
3. Integration of Technologies
Integrate vibration and oil analysis technologies by setting up the necessary equipment and software systems. Choose tools that can interface with each other to allow for easier data correlation and analysis. For instance, software that can compile data from both vibration sensors and oil analysis reports into a single dashboard will provide a more comprehensive view of machine health.
4. Establish Routine Monitoring
Develop a routine monitoring schedule that includes regular checks using both vibration analysis and used oil analysis. The frequency of these checks can vary based on the criticality of the equipment and past maintenance records. Critical machinery might need more frequent monitoring, while less critical systems may require less frequent checks.
5. Data Analysis and Reporting
Implement robust data analysis procedures to ensure that the data collected is used effectively. Develop standardized reports that highlight key metrics and trends. Use predictive analytics to forecast potential failures before they occur, allowing for proactive maintenance and repairs.
6. Continuous Improvement
Adopt a continuous improvement approach by regularly reviewing the effectiveness of the maintenance program. Update your practices based on new insights and advancements in predictive maintenance technologies. Encourage feedback from the maintenance team, as their firsthand experience can provide valuable insights into the practical aspects of the program.
7. Stakeholder Engagement
Keep all stakeholders informed about the changes and benefits of the enhanced reliability program. Regular updates, whether through internal reports, meetings, or newsletters, will help maintain alignment and support for the initiative. Highlight successes and learnings from the program to promote its value and encourage continuous support.
8. Compliance and Safety Standards
Ensure that all practices comply with industry safety and quality standards. Regular audits and compliance checks should be part of the program to maintain high standards and avoid potential legal or operational risks.
Conclusion
By effectively implementing an enhanced reliability program that synergizes vibration analysis and used oil analysis, organizations can expect a significant improvement in equipment uptime, reduced maintenance costs, and overall enhanced operational efficiency. The key to success lies in careful planning, skilled execution, and ongoing management of the program to adapt to new challenges and technologies.