Condition-Based Maintenance and Oil Analysis
The Role of Oil Analysis in Condition-Based Maintenance
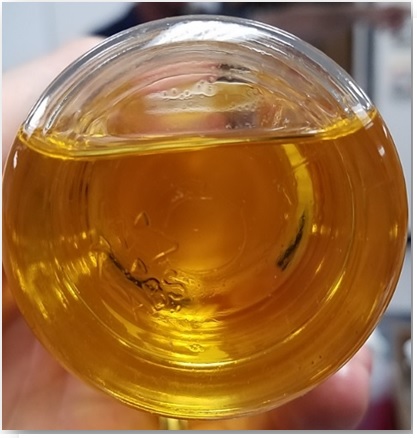
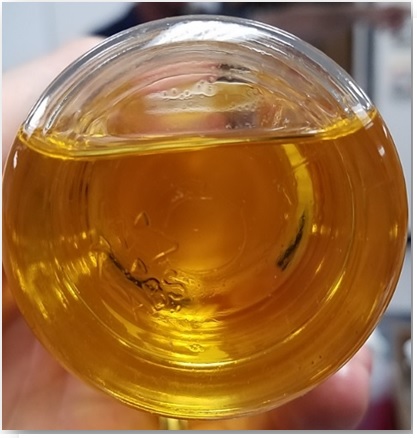
Introduction
What is condition-based maintenance (CBM) and why integrate into your reliability program? Preventative maintenance (PM) is the traditional maintenance approach. Maintenance such as oil changes are performed on a set interval. The drawback to this approach is that the oil and machine condition is not considered. The oil may be changed before it is necessary, or the life of the oil has been overextended. Changing the oil prematurely results in wasted money on labor, material costs and unnecessary downtime. Overextending the oil change may result in degradation and deposits forming in the lube system and damage to critical machine components. Condition-based maintenance provides a solution to this problem.
Condition-based maintenance captures data from machine and lubricant monitoring techniques to determine when to perform maintenance. Let us compare the two maintenance methodologies. Figure 1 demonstrates how performing maintenance when conditions indicate that maintenance is needed can result in less downtime and increase machine availability,
Figure 1
Choosing a Maintenance Strategy
Condition-based maintenance is an important part of a complete reliability-based maintenance program. The opposite end of the maintenance strategy of CBM is run-to-failure. This method involves running equipment until it fails. How do we decide when to use CBM, and do we apply it to everything?
There are several factors that come into play for when to choose a CBM strategy: (1) a meaningful volume of machine fluid in use, (2) machine criticality, (3) and the all-encompassing, total cost of downtime. Table 1 lists the major factors to consider when making this decision.
Table 1
The Role of Oil Analysis in Condition-Based Maintenance
Oil analysis is a cornerstone of the CBM strategy. Oil analysis provides vital information in three key categories: machine condition, oil condition, and contamination.
· Wear: Oil analysis can detect minute amounts of metal particles that enter the oil due to normal wear or early signs of component damage. The presence of metals such as iron, copper, or aluminum can indicate abnormal wear or impending failure, prompting timely maintenance actions before severe damage occurs.
· Contaminant ingression. Alongside wear metals, oil analysis detects contaminants such as dirt, water, and chemical impurities. Contaminants can accelerate wear and lead to corrosion. By monitoring these levels, maintenance teams can determine if the operating environment or machine seals are compromised and adjust maintenance schedules accordingly.
· Lubricant degradation: Over time of normal use the oil oxidizes, and by-products such as acids and sludge form. These degradation products can affect the oil’s lubricating qualities and lead to increased wear and corrosion. Oil analysis measures indicators such as the acid number and sludge content, allowing maintenance teams to plan oil changes or other interventions before these by-products cause damage. More on this later in this blog post.
Advanced Oil Analysis
Below are a few examples of advanced oil analysis techniques that provide additional information when a potential problem is detected by oil analysis or another methodology.
· Ferrography: is an advanced analytical technique involving microscopic particle evaluation, used in oil analysis to evaluate wear debris and contaminants within lubricating oils. It involves the collection and examination of ferromagnetic particles that have been deposited onto a specially prepared slide or film.
· Linear Sweep Voltammetry: An electrode is inserted into a prepared solution of the oil and the voltage is linearly increased and the response is measured. This technique is used to measure the remaining antioxidants in the oil as a percentage relative to the new oil.
· MPC (Millipore Filter Colorimetry): The fluid is mixed with a nonpolar solvent, which is then passed through a filter membrane. Degradation by-products are insoluble and are deposited onto the filter membrane. The membrane color is a measure of the amount of degradation products in the oil.
· RPVOT (Rotating Pressure Vessel Oxidation Test): The oil is placed in a container which is pressurized with oxygen. Water and a copper coil are placed in the container. The vessel is then heated. These conditions accelerate the oxidation of the oil. A specified drop in the pressure indicates the end of the test. The result is reported in minutes.
There are many more tests that are available to measure wear, contamination and fluid condition. Your laboratory can help you determine the specific tests that will be most beneficial to your specific machine and operating conditions.
Data-Driven Maintenance Decisions
· Trend Analysis and Predictive Insights: By regularly sampling with a structured oil analysis program, maintenance teams collect valuable historical data. This data can be used to establish trends, identify recurring issues, and predict potential failures. With advanced statistical or machine learning tools, these trends can be analyzed to forecast when a machine component might fail, enabling maintenance to be performed only when necessary.
· Optimizing Maintenance Schedules: Instead of relying on time-based or mileage-based maintenance, oil analysis supports a more dynamic and efficient maintenance strategy. It enables organizations to switch to condition-based maintenance, where interventions are scheduled based on the actual condition of the equipment rather than predetermined intervals. This not only reduces unnecessary maintenance activities but also minimizes downtime and extends equipment life.
Enhancing Overall Operational Reliability
· Risk Management: By detecting issues early, oil analysis helps reduce the risk of catastrophic failures. This is especially critical for machines that are vital to operations, where unexpected breakdowns could lead to significant production losses or safety hazards. Early intervention ensures that repairs are less extensive and more cost-effective.
· Cost Efficiency: Proactive maintenance informed by oil analysis avoids the excessive costs associated with unplanned downtime, emergency repairs, and potential equipment replacements. It allows for maintenance budgeting to be more predictable and aligned with actual equipment needs, rather than based on routine schedules that might not reflect real wear and tear.
Integration into a Comprehensive CBM Program
· Complementary to Other Monitoring Techniques: While oil analysis provides detailed information about the chemical and physical condition of the lubricant, it is often used alongside other diagnostic tools—such as vibration analysis, thermography, and acoustic emissions—to offer a holistic view of machine health. This multi-faceted approach improves the accuracy of maintenance predictions.
· Feedback Loop for Continuous Improvement: The data generated by oil analysis feeds back into maintenance planning and operational strategies. It enables continuous improvement in both maintenance practices and operational performance, fostering an environment where reliability and efficiency are constantly enhanced.
Conclusion
Oil analysis is an indispensable tool in a condition-based maintenance strategy. It provides early detection of wear, contamination, and lubricant degradation, enabling maintenance teams to intervene before minor issues evolve into major failures. Through trend analysis and predictive maintenance scheduling, oil analysis not only improves equipment reliability but also optimizes maintenance costs, contributing significantly to the overall efficiency and longevity of industrial machinery.
In conclusion, integrating oil analysis into your maintenance program transforms reactive, time-based approaches into a dynamic, data-driven strategy. This proactive methodology minimizes unplanned downtime and expensive repairs, while extending the life of your equipment through timely interventions. As industrial operations continue to evolve, leveraging oil analysis and CBM is key to maintaining a competitive edge, ensuring safety, and achieving long-term operational success.
Unlock the full potential of your maintenance strategy with our cutting-edge oil analysis solutions. Contact us today to learn how our tailored CBM programs can reduce your maintenance costs, improve equipment performance, and keep your operations running smoothly. Contact the laboratory and talk to one of our STLE/ICML certified analysts. Let us help you turn data into actionable insights for a more efficient and profitable future.