Catastrophic Bearing Failure - A case study In why sampling location is critical to successful oil analysis.
This is a case study emphasizing the importance of collecting oil samples at the optimal location of a circulating lube system so abnormal equipment wear is detected at the earliest stage.
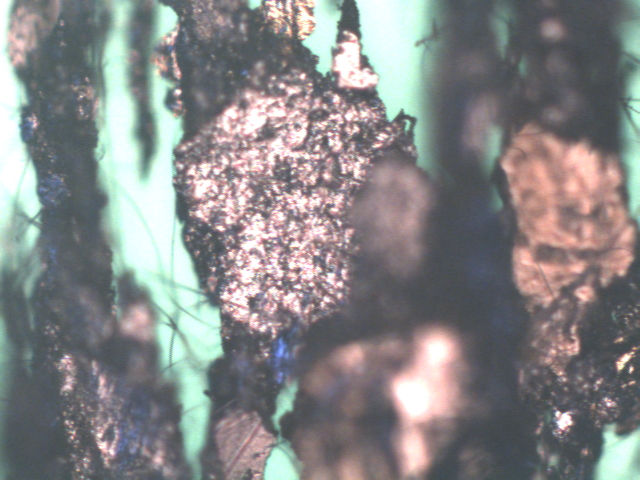
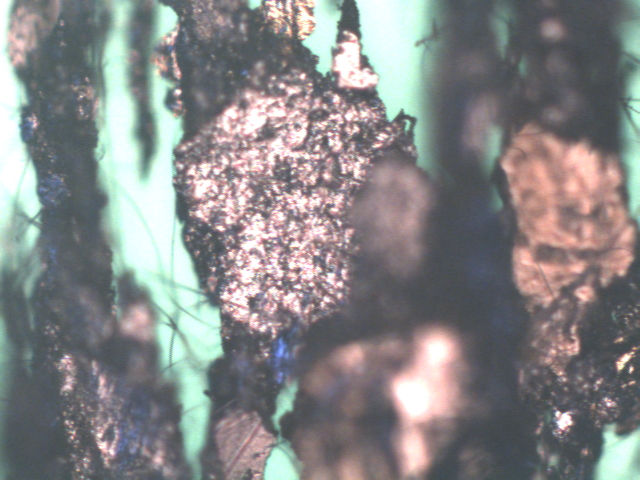
Last week an MRT customer lost a critical compressor due to unexpected bearing failure. The customer diligently mails in lube oil samples for routine analysis on a monthly or bi-monthly basis. Why didn’t the oil analysis detect early stage abnormal bearing wear in advance of this unexpected failure? Isn’t that what oil analysis is for, to catch abnormal wear issues at the earliest stage?
It’s an understatement to say that it’s frustrating when this happens. Together let’s review recent oil analysis results as the unit approaches failure in late September. See an abbreviated set of data from the five most recent lube oil samples and a filter sample completed after the failure.
Relevant Observations of each sample’s test results
Sample 1 from April 2020 has visible debris particles that are >40 microns in size. Oil condition is normal. There’s 2 ppm of iron, but no ferrous magnetic debris detected and no other wear metals or contaminant metals detected. No indication of abnormal equipment wear according to these oil analysis tests. Continue use of oil. Filter the oil to remove the visible debris and re-sample in one month to monitor for an improvement in cleanliness.
Sample 2 from July 2020 has an elevated ISO 4406 particle count result, but that is actually an improvement in cleanliness compared to the sample from April since there’s no visible debris to the naked eye. Only 1ppm of iron and no other wear metal elements detected. No indication of abnormal equipment wear. Oil condition is normal. Continue use of oil and continue to filter the oil. Re-sample in one month to monitor for an improvement in cleanliness.
Sample 3 from August 2020. Noticeable improvement in oil cleanliness! Looking good – the oil is cleaning up and all other test results are normal. No wear metals and no ferrous debris detected. No indication of abnormal equipment wear. Continue use of oil and continue to filter the oil. Re-sample in one to two months.
Sample 4 from September 2020 is similar in condition and cleanliness to Sample 3. The particle count has leveled off. The ISO 4406 remains moderately elevated. The oil could be cleaner, but there’s still no indication of an abnormal wear issue THAT IS ALREADY OCCURING!
Unfortunately, the active abnormal wear condition remains undetected by oil analysis. Why?
Sample 5 from October 1, 2020 is a postmortem / post bearing failure oil sample taken from the filter housing. Severe concentrations of various wear metal elements in the oil. Over 20,000 ppm of magnetic debris in the oil sample taken from the filter housing location. The uncirculated oil in this housing is dark in color from the extreme level of debris present. See one microscopic image of wear debris in the sample.
The sample contains large ferrous abrasive and fatigue wear particles (100+ microns in size). These particles were likely generated during, or immediately prior to, equipment failure. Many ferrous rubbing wear and large (60+ micron) ferrous fatigue wear particles were present, which appeared oxidized and/or corroded. These particles were likely generated prior to equipment failure.
Sample 6 from October 1, 2020 is a postmortem filter analysis. The filter is loaded with wear debris. See the metal coated to the filter media.
What happened? Why didn’t the oil analysis catch this earlier, by detecting microscopic wear particles ripping and rubbing off a bearing? By the way, not until one or two days before the failure did the unit begin to vibrate aggressively. Vibration readings did not detect this issue either, nor were there elevated bearing temperature readings.
Unfortunately, this is an extreme example of the danger of sampling a circulating oil at a location that is downstream of the filter. All the oil samples taken prior to the bearing failure are from a location after the filter (an example of sampling bias). This issue would have been detected by the oil analysis if the sample port was located downstream of the bearings and upstream of the filter. The filter analysis confirms this, since a meaningful percentage of the wear debris is darkened from oxidation – meaning it was ripped and rubbed from the bearing some time ago.
Please use this case study as motivation to survey your plant to list all the critical lube system sampling locations that are downstream of filters. We highly recommend scheduling the work to optimize the sample ports locations to avoid this issue happening to you. In the short term if a sample location cannot be changed then we recommend an annual filter analysis on each critical lube system.