What is Varnish?
Varnish is an increasingly prevalent issue for operators of rotating equipment. In this article, we answer fundamental questions on varnish, such as its causes and effects. Also, we discuss methods for varnish detection.
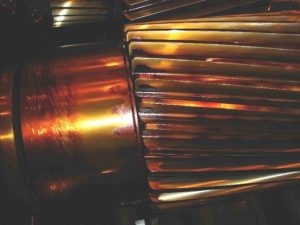
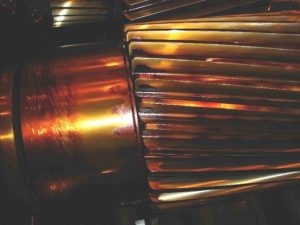
Varnish occurs when a lubricant degrades and produces by-products, which accumulate in the lube system. These degradation by-products are dissolved in the lubricant until it becomes saturated. Once the lubricant is saturated, these by-products can agglomerate and then adhere on metal surfaces to form varnish. Varnish formation is dependent on factors such as temperature, pressure, flow properties, fluid solvency, and base oil chemistry.
What causes varnish?
The three most common causes of varnish are:
- Oxidation: chemical breakdown of the oil that occurs in the presence of oxygen. Oxidation occurs gradually under normal, mild operating conditions after the antioxidant additives are depleted. However, the rate of oxidation accelerates as temperatures increase. Typically for every 10°C (18°F) increase in operating temperature, the rate of oxidation doubles (Arrhenius Rate Rule).
- Thermal degradation: a similar process that occurs without the presence of oxygen. Thermal degradation occurs because of adiabatic compression from entrained bubbles or when the oil encounters hot surfaces greater than 200°C (400°F). Adiabatic compression occurs when air bubbles rapidly implode due traveling from low pressure to high pressure. The implosion increases the oil’s temperature to greater than 1,000°F, which is sufficient to thermally degrade the oil.
- Foreign contaminants: Contamination in the oil can be a primary constituent of varnish, or it can be present as inclusions in existing soft contaminant formations.
These degradation processes are accelerated by:
- Heat
- Water
- Oxygen
- Metal catalysts such as copper, zinc, and iron
- Organic acids
The processes that lead to varnish formation.
Why is varnish a problem?
Varnish can impact equipment operation in many ways:
- Increases the rate at which the oil degrades, which reduces the oil’s service life. Varnish degrades a lubricant by an autocatalytic reaction which accelerates degradation as free radicals and temperatures increase.
- Decreases the oil’s ability to dissipate heat. Varnish can form an insulating layer on heat exchangers and reservoir walls which prevent them from properly transferring heat. This can increase the temperature of the oil and lead to further degradation. It can also reduce heat transfer from critical components such as bearings, which can lead to premature failure.
- Reduces clearances in critical components, such as, spools, bearings, servo valves, and last-chance filters (LCFs). The solvency of varnish in turbine oil is temperature dependent. When temperatures fall below certain thresholds in the hydraulic control section of turbines, the formation of deposits can occur on the control valves. This can lead to sticking and malfunctioning of tight clearance moving parts.
- Interferes with proper lubrication, which promotes wear. Varnish can impede the flow of critical oil pathways which can cause metal to metal contact. Varnish also attracts abrasive dirt and solid particles which can increase wear.
As mentioned before, base fluid chemistry has a significant impact on the propensity of a fluid to form varnish. Certain Group V (synthetic) formulations utilize glycols or esters for the base fluid, which can have radically different varnish-forming properties than traditional mineral oils. Some of these base oil formulations may even claim to be varnish-free. However, it is important to note that varnish formation is a complex process, with interplays between temperature, pressure, moisture content, flow properties, and many other parameters. We would recommend that you do not take it for granted that your oil cannot varnish!
Soft contaminant levels (varnish), compared to fluid appearance.
Varnish CANNOT always be detected by routine lubricant analysis tests, such as appearance, color, acid number, viscosity, and particle count.
How to detect varnish proactively?
- Determine the Remaining Antioxidant Levels (RULER): Remaining Useful Life Evaluation Routine (RULER) determines the levels of antioxidants remaining in the oil. Antioxidants control the rate of oxidative degradation. Oxidation is the primary degradation route for turbine oils. When antioxidants are depleted, rapid degradation can occur.
- Measure Varnishing Potential of the lubricant (MPC): Membrane Patch Colorimetry (MPC) determines the concentration level of compounds in a lubricant that are precursors to soluble and insoluble varnishes. This test is effective at detecting the varnish potential before problems occur.
- Ultra-Centrifuge (UC) to look for sub-micron insoluble particles: Insoluble contaminants can be high in concentration in a used lubricant, although undetected through routine particle counting techniques. The UC creates an elevated angular velocity of a lubricant sample that causes sub-micron insoluble contaminants to accumulate for measurement.
MRT Laboratories has the capability to perform the above tests, and much more. If you'd like to learn more about Advanced Testing, please check out this link.
How often to test for varnish?
Testing frequency depends on:
- Unit criticality: critical systems should be tested more often.
- Unit age: new units should be tested more frequently during break‐in (first 6 months).
- Fluid age: fluids should be tested more frequently when they begin to approach the end of their service life.
Testing should be done within 1 month after varnish mitigation to validate a successful removal.
Typical testing intervals are every 3 to 6 months. This should be determined by the severity of the system after the first round of testing.