MRT Laboratories and the Value of Oil Analysis
The successful oil analysis program considers several aspects – goal, training, sampling, data interpretation, and action.
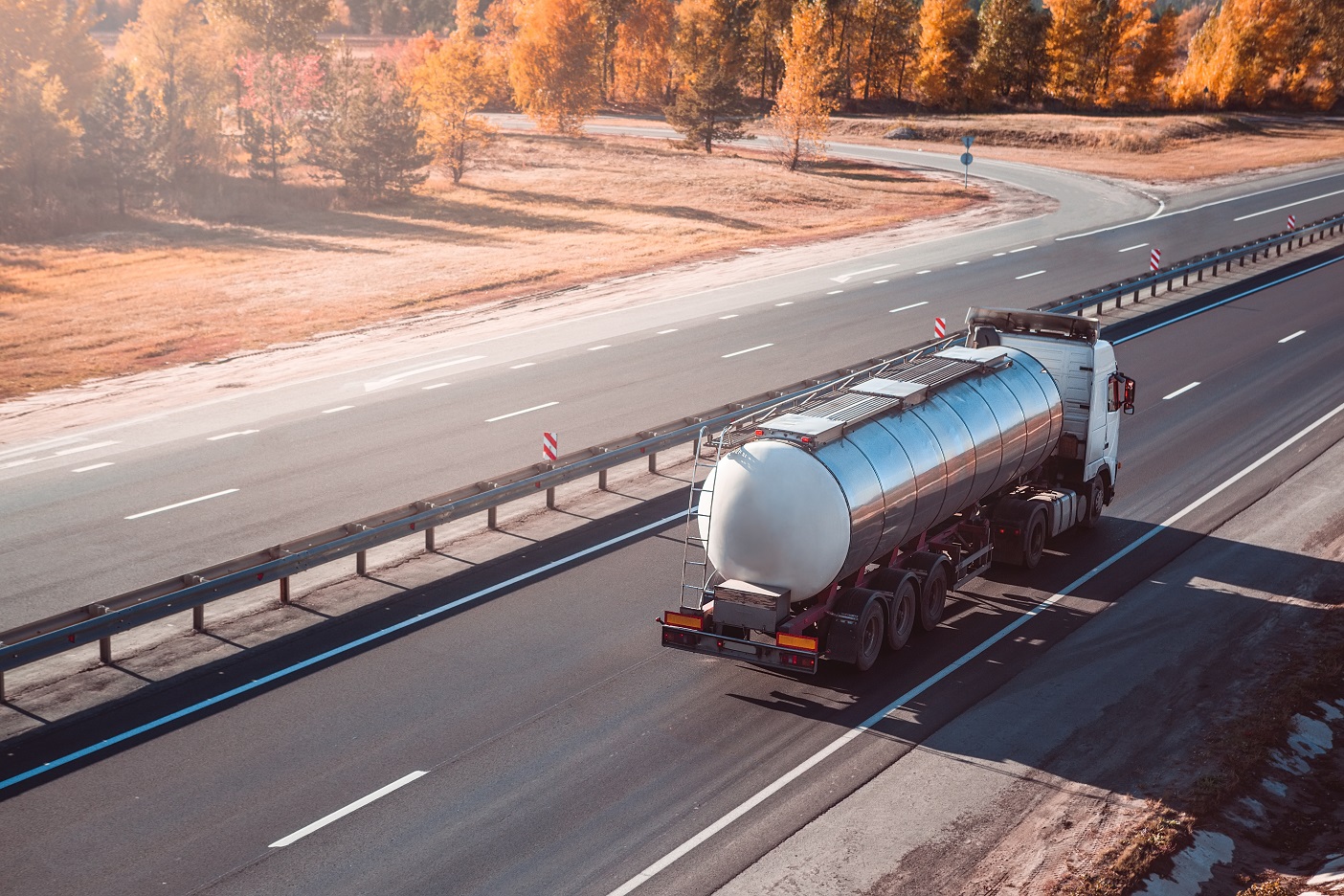
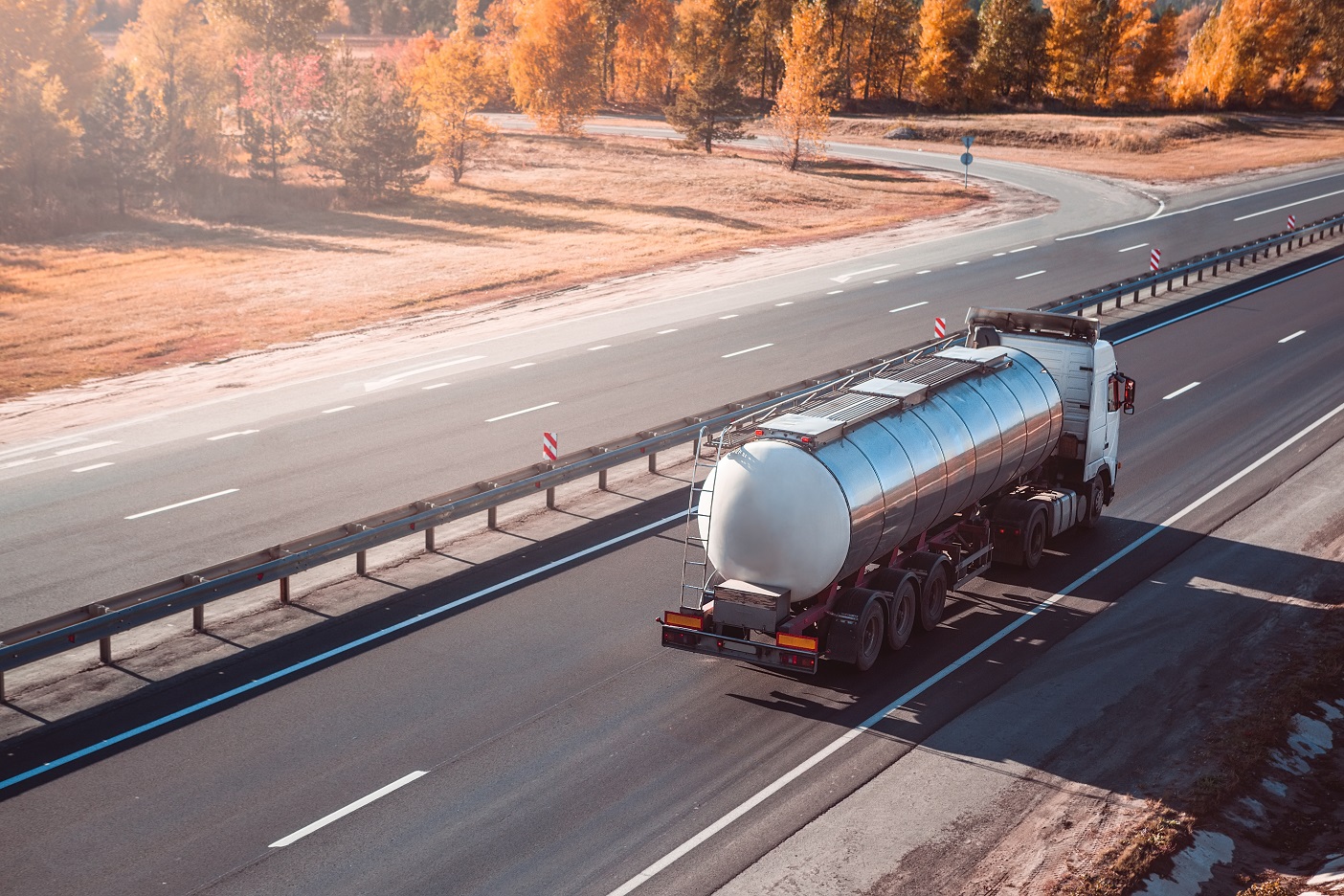
MRT Laboratories and the Value of Oil Analysis
By Michael D. Holloway of 5th Order Industry and Ben Hartman of MRT Laboratories
Many companies use oil analysis unfortunately not all companies take full advantage of what oil analysis can provide. The successful oil analysis program considers several aspects – goal, training, sampling, data interpretation, and action. Establishing the goal for an oil analysis program can be the most difficult. Before goals are set, it is important to understand what oil analysis can provide. Simply put, an oil analysis program can help establish fluid management, predictive maintenance, strategic sourcing, operational effectiveness, and even research and development.
How Oil Analysis Contributes to Fluid Management
Oil analysis provides data on the serviceability of the fluid forming insight into the performance of the lubricant in the components which has a direct influence on the spend profile. Dissolved or emulsified water can be identified which provides information on how well the oil will shed water. Oil analysis data can help in optimizing change intervals.
Predictive Maintenance
Abnormal machine wear behavior is identified which helps with maintenance planning which leads to the elimination of repetitive problems towards driving increased reliability. Using this data helps with root cause analysis and equipment lifetime projections.
Strategic Sourcing
Making a decision on which oil to buy through oil analysis has been a tool employed from the onset. Yet only recently have companies begun using oil analysis data to audit procurement of not only their lubricants but also the various components and filters. Premature wear is identified through the elemental analysis.
Operational Effectiveness
The proper operation and uptime of an asset has a direct influence on the quality of the end product. If the hydraulics experience cavitation or sluggish behavior due to an oil issue, the end product may suffer. Oil analysis has a direct influence on the quality control due to the fact that the lubricant influences the operation of the asset. Using oil analysis supports a continuous improvement initiative. Complying with or administering a warranty will often require empirical evidence. Oil analysis has been used by end-users and OEMs alike for warranty programs.
Research & Development
Often a lubricant, component, or equipment manufacturer will test their products in a simulated environment in order to produce data for formulation or part enhancement. When an end-user practices oil analysis, that data can become very useful in order to understand how well a formula, part, or machine is performing in a real application.
Getting Started
Practicing oil analysis requires proper sampling. The task must be repeatable, no matter who collects the sample. The process must remain the same with emphasis on reducing as much opportunity for outside contamination as possible. The goals must be established for a specific purpose and Key Performance Indicators put in place. Oil analysis provides valuable data concerning wear debris, contaminants, organic matter, and the oil condition. The process must be accurate so that it may reflect the current lubricant and machine condition. Over a period of time, a strategic wear pattern can be developed leading to a more accurate prediction model. Basic requirements for optimizing an oil analysis program will include synchronizing the oil analysis data along with maintenance records, establishing limits for wear, contaminants, oil life, and performance of the oil. This will help in targeting optimizing drain intervals. In the submissions that follow, there will be an examination of the tests run as well as the data interpretation of results for:
· Wear Metals
· Viscosity / Flow
· Contamination
· Performance Chemistry
Oil analysis has become an integral tool for many organizations. Find out how MRT Laboratories has helped improve equipment effectiveness through an oil and equipment condition monitoring program.
Next Submission:
Are metals in an oil sample coming from mechanical wear via surface contact? Is it corrosive wear? Is it additive chemistry? Is it contamination? Let’s find out!…