External Metal Sources: Their Negative Influence on Lubricated Systems
Abrasive metal contamination leading to component failure through surface wear
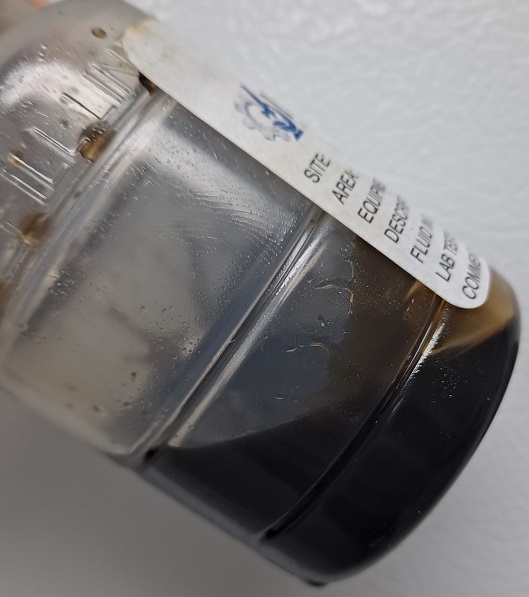
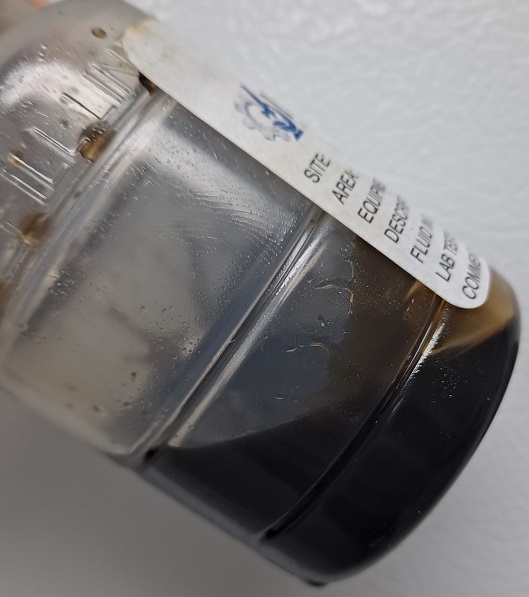
By Michael D. Holloway, 5th Order Industry and Ben Hartman, MRT Laboratories
The major contributor for component failure is external contamination in the form of sand or soil (dirt). A leading cause for failure is surface wear from abrasive materials. Abrasive materials find their way into a lubricated system through several ways, including contaminated lubricants, unclean application methods, exposed reservoirs, and compromised seals. Abrasive particles wear surfaces by inserting into the space tolerance between two sliding, lubricated surfaces or as an erosive agent in a highly turbulent system. Abrasive particles are typically hard metallic contaminants.
Metallic elemental analysis can help in understanding the physical nature and chemical structure of contaminants and proven valuable in oil and equipment condition monitoring. Understanding the particle shape and size, as well as the chemical signature can help determine the source and root cause of wear. Dirt and sand are major sources of wear. Sand is Silicon Dioxide (SiO2) with distinctive particles between 10µm to 2mm in diameter. Dirt is composed of minerals, water, gases (air, CO2, Methane), organic matter, and microorganisms. The mineral, air, and water concentrations vary from 2% to 50% each, depending upon origin. Organic matter from decayed animals and plant can make up to 25% and microorganisms can be found up to 5% by volume. All five components of dirt can contribute to failure opportunities in equipment with minerals offering the largest contribution.
Minerals have distinct elemental signatures defined as naturally occurring homogeneous elements or inorganic compounds with a chemical composition and characteristic geometric molecular shape. There are two fundamental types of minerals: Primary and Secondary.
Primary Minerals formed from the crystallization of molten magma. This type of mineral has persisted with little change in composition since they were extruded in molten lava such as Quartz (SiO2), Feldspar (KAlSi3O8), Biotite (KMg3AlSi3O10), Albite (NaAlSi3O8), Muscovite (KAL3Si3O10) to name a few. Primary minerals are most prominent in sand and silt fractions. Silt is granular material of a size between sand and clay and composed mostly of broken grains of quartz with particles typically between 2µm to 30µm in diameter.
Secondary Minerals are formed on the Earth’s surface by the weathering of Primary Minerals. These minerals are composed of silicate clays and iron oxides and have been formed by the breakdown and weathering of less resistant minerals. Common examples of these minerals would be Goethite (Fe3O(OH)), Hemacite (Fe2O3), Calcite (CaCO3), Gypsum (CaSO4), Dolomite (CaMgCO3), and Clay composed of Aluminum Silicates with particles <4µm in diameter.
Understanding what makes up minerals, as well as their concentration ratios, help to determine the origin of the metals. Elemental oil analysis through Inductive Coupled Plasma (ICP) or Rotrode Emission Spectroscopy (RDE) will only provide information of the concentration in parts per million of various metals without providing the molecular signature. Unless a sample is digested with hydrofluoric acid, particles greater than 7µm will not have enough residence time in the instrument to provide a completely accurate concentration. Using X-ray diffraction will provide molecular information without particle size restriction, yet reference standards are required. If a sample contains iron, the ICP will indicate ppm of Fe whereas the X-Ray Diff can discern between molecular structures such as wear debris or external contamination.
Metals not only represent the source and result of wear, but they also contribute to the formation of acids (Fig. 1). Acid generation in lubricated systems will lead to the development of sludge, varnish, and lacquer due to the free-radical generation, followed by the propagation of larger molecules, and terminating with highly crosslinked polymers. The synthesis route for sludge is a coordination free-radical polymerization. This form of polymerization is also a common process to manufacture useful plastics. Metallocene catalysts that assist in plastics production are similar in functionality to the metal ions that are typically found in used oil. Understanding and eventually controlling metallic concentration in the lube system will lead to increased reliability through reduced failure.
Figure 1. The Catalytic Effect of Metals and Water in the Formation of Acids
Ref: Lubricant Deterioration in Service, E. Abner, Vol 1, pg. 518 CRC Handbook of Lubrication
Metals have a significant contribution to the demise of an asset. Water contamination plays a synergistic role when combined with metals. The next submission will examine how water jeopardizes the function of a lubrication system.