Anticipate Alloy Corrosion Potential Using the Voltage Index
How to avoid corrosion of multi-metal alloys, and Why You Never Should Mix Your Tableware in the Dishwasher
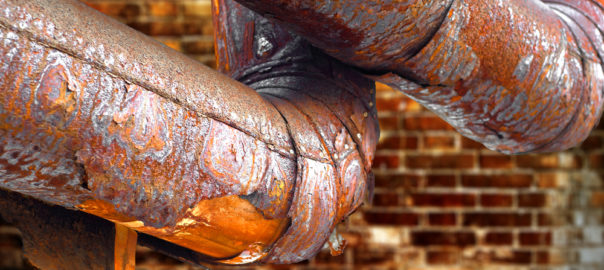
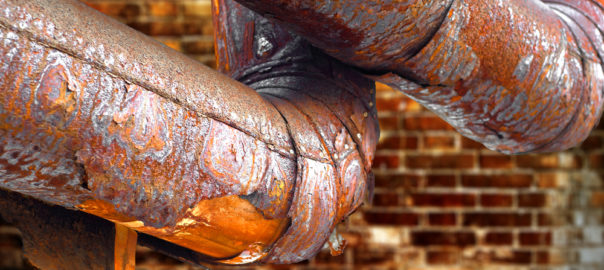
By Michael D. Holloway, 5th Order Industry and Ben Hartman, MRT Laboratories
Entry level chemistry students learn Entropy – how every system is always trying to achieve its most comfortable state of existence. That concept holds true for societies, companies, families, animals, and even molecules and atoms. All things are in a constant state of change. All things are working towards their ‘Enthalpic Goal’. Metal is no different. Metals can be pure elemental (Iron, Aluminum, Copper, etc.…) or combinations forming alloys (Brass, Bronze, Stainless Steel, etc.,,,). Metal is normally present in a stable oxidized form as ore. These metal ores tend to react with water or oxygen to form corresponding metal oxides. This process leads to deterioration known as corrosion. While the metal achieves a ‘comfortable state’ it no longer has certain physical characteristics we find useful such as strength, durability, ductility, and even conductivity. The metal has experienced corrosion.
In a 2016 study conducted by the NACE (formerly known as the National Association of Corrosion Engineers) and outlined in their publication “The International Measures of Prevention, Application and Economics of Corrosion Technology (IMPACT),” corrosion is responsible for a global cost of $2.5 trillion dollars. This figure represents roughly 3.4 percent of the global Gross Domestic Product (GDP).
Corrosion can be further defined as being Dry or Wet. Dry Corrosion occurs when oxygen reacts with the metal without the liquid. While dry corrosion is not as harmful as wet corrosion, it is temperature sensitive. Exposing a clean piece of metal to an open flame will quickly form an oxide layer. The formation in certain metals may lead to the reduction of the rate of corrosion. This layer acts as a barrier for further oxidation. This is known as Passivation. This is common in many alloys and certain metals. Copper and aluminum form a protective oxide layer or scale. This will slow down oxidation and ultimately corrosion. Stainless steel has chromium which helps form a protective layer that prevents further corrosion. Unfortunately, not all oxide layers form a protective layer. If the oxide layer is not continuous, it will not be able to reduce the amount of oxygen reaching the metal surface.
Wet corrosion is also known as Galvanic Corrosion. This form of corrosion (also known as bimetallic corrosion) is more dangerous than the dry type. Here, an electrochemical cell is produced consisting of an Anode (negative charged metal), a Cathode (positive charged metal), and an Electrolyte solution that allows for electron transference. Ground water or sea water is a common electrolyte and is responsible for the majority of metal corrosion. The movement of electrons from the anode to the cathode starts an oxidation reaction at the anode that causes it to degrade. This type of corrosion is affected by the magnitude of electric potential created. To determine the severity of the potential corrosion, you would have to look at the metal’s potential in a galvanic series table. This is where corrosion engineers will determine the rate of corrosion at the metal surface. One metal experiences corrosion (loses electrons), while the other will not normally corrode when in proximity. This doesn’t mean that it will not corrode because often it will, just not at the same rate, conditions or mechanisms. Cathodic metals (positive charged metals) corrode when in proximity to anodic metals (negative changed).
When two dissimilar metals are put in proximity of each other, it is essential that we contemplate their anodic index. The anodic index is a measure of the electrochemical voltage that will be developed between the metals. When two metals are in proximity and an electrolyte provides separation, a voltage potential is created. This is how the first batteries were developed. To find the relative voltage of a pair of metals we subtract their anodic indices. By doing so, one can calculate the voltage potential that can be generated. This also provides insight into the galvanic corrosion response. The greater the generated potential, the greater the galvanic corrosion. Consider the following table of metals and their Voltage Index (V):
Ref: Handbook of Corrosion Engineering, Pierre R. Roberge, McGraw-Hill; 2000
According to the Handbook of Corrosion Engineering, to reduce galvanic corrosion for metals stored in normal environments such as storage in warehouses or non-temperature and humidity-controlled environments, there should not be more than 0.25 V difference in the anodic index of the two metals in contact. For controlled environments in which temperature and humidity are controlled, 0.50 V can be tolerated. For harsh environments such as outdoors, high humidity, and salty environments, there should be not more than 0.15 V difference in the anodic index. For example: gold and silver have a difference of 0.15 V, therefore the two metals will not experience significant corrosion even in harsh conditions.
If dissimilar metals must come in contact due to design, the difference in anodic index is often managed by finishes and plating. The finishing and plating selected allow the dissimilar materials to be in contact, while protecting the cathodic metals from corrosion by the anodic metal. The metal with the most negative anodic index will corrode. A real-world example would be why sterling silver and stainless-steel tableware should never be put in a dishwasher at the same time. The steel items will corrode. The soap and water provide an electrolyte solution that will increase the galvanic corrosion of the metals.
Thank you so much for reading!! In our next installment, we will explore the several different types of corrosion that can occur in a lubricated system.