Understanding Lubrication Regimes to Maximize Equipment Run-Time
Select a proper lubricant based on your equipment's lubrication regime
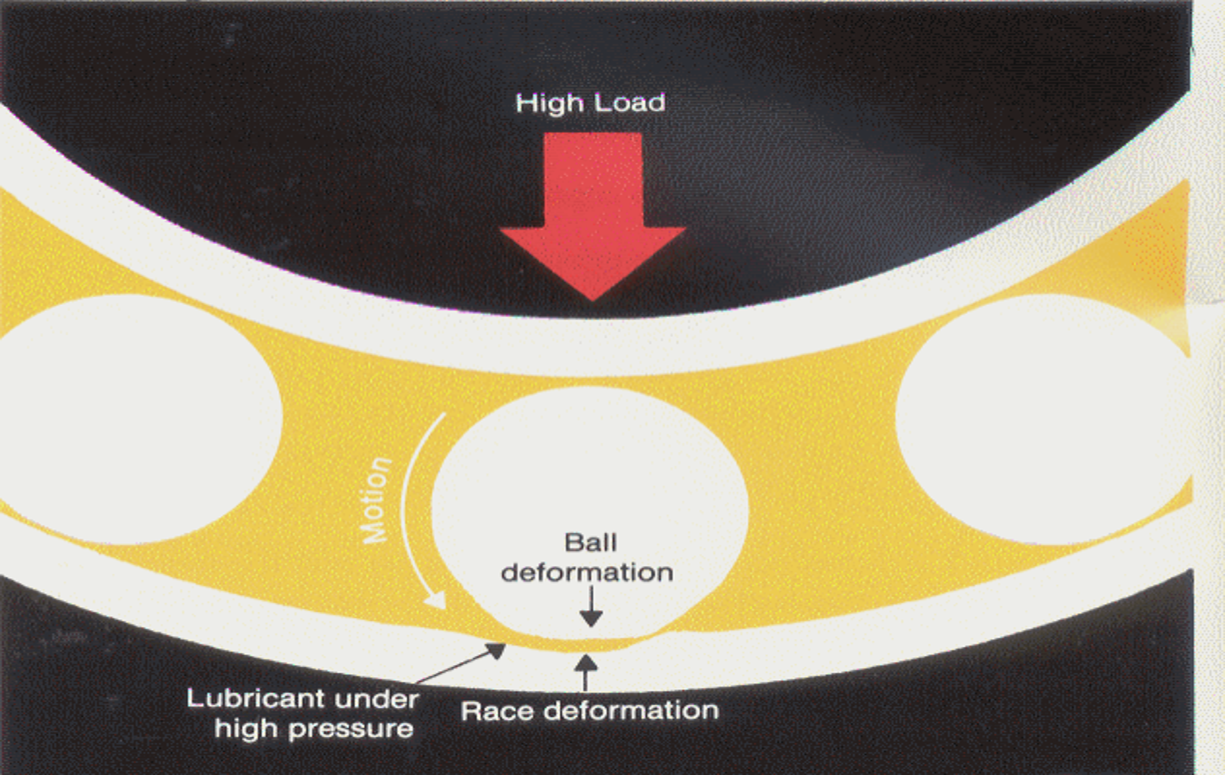
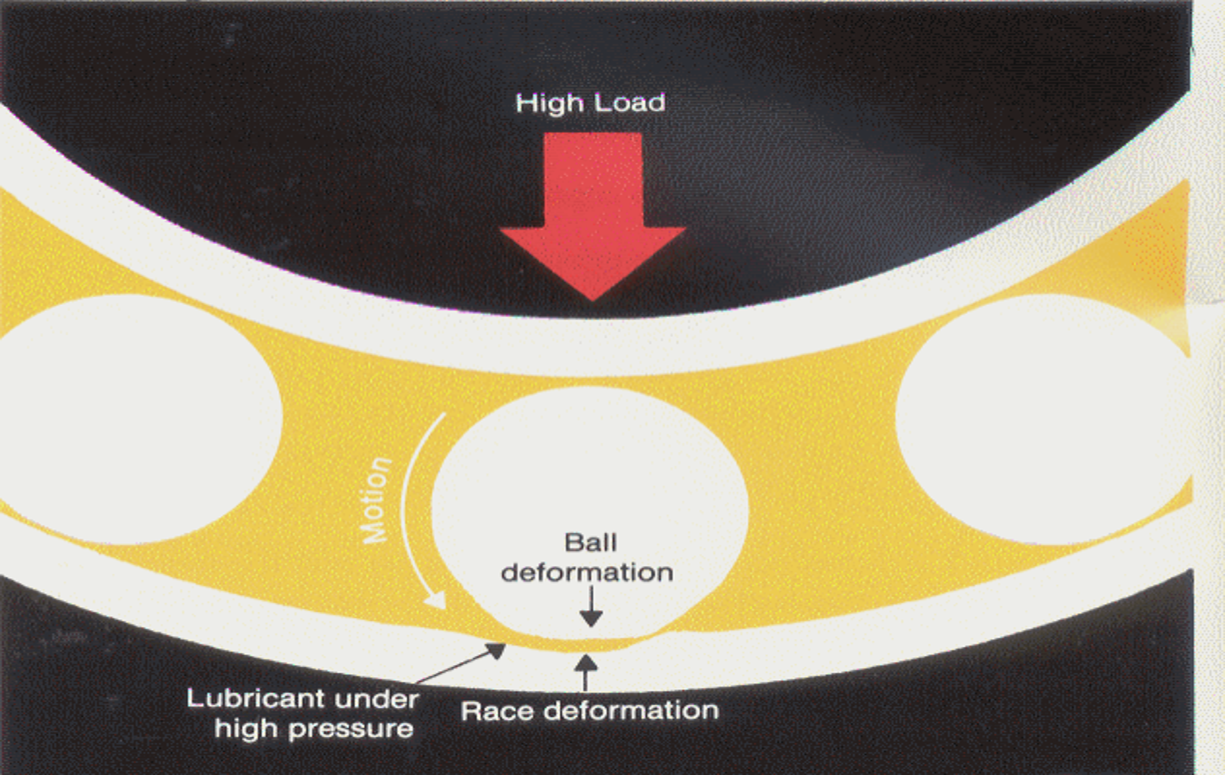
Introduction
A lubrication regime is the type of lubrication layer between two metal surfaces that can come in direct contact with one another. A lubrication regime can be either boundary, mixed, or full-film lubrication. Deciding the proper lubricant for an application requires determining which lubrication regime or regimes occur during equipment operation. Understanding these regimes is essential to minimize damage from metal-to-metal contact, selecting the right lubricant and additives to optimize the performance, reliability, and longevity of mechanical systems.
Different machinery types operate under varying lubricating conditions. For example, journal bearings in electric motors rely on full-film hydrodynamic lubrication, where a fluid film separates the metal surfaces and there is no metal-to-metal contact during running operation. On the other hand, gears, especially under heavy loads, can experience physical contact between the interacting gear teeth while in boundary and mixed lubrication regimes.
By understanding the characteristics and mechanisms of these lubrication regimes, we can make informed decisions when choosing lubricants and additives. We will explore each regime's unique features, mechanisms, and applications.
Boundary Lubrication
Boundary lubrication is a lubrication regime that occurs when there is direct contact between two surfaces (at times >90% metal-to-metal surface contact1), and a thin film of lubricant is unable to separate the metal surfaces from rubbing against each other. Boundary Lubrication has by far the highest coefficient of friction amongst the regime types. In this regime, the primary function of the lubricant is to minimize friction and wear by forming a protective boundary film on the surface.
Characteristics of Boundary Lubrication:
1. Thin lubricant film: The lubricant film in boundary lubrication is extremely thin, often in the range of just a few molecular layers. This thin film is not sufficient to provide complete separation between the surfaces.
2. Direct surface-to-surface contact: The surfaces in contact experience significant load and can come into direct contact with each other, leading to higher friction and wear.
Mechanisms of Lubrication
Boundary lubrication relies on several mechanisms to reduce friction and wear:
1. Boundary film formation: The lubricant forms a protective film composed of additives, such as anti-wear and extreme pressure agents, which adhere to the metal surfaces. We will discuss additives in more detail in a future blog post. This boundary film acts as a barrier, preventing direct contact between the surfaces.
2. Adsorption and chemical reaction: The lubricant molecules adsorb onto the surface, creating a monolayer that reduces friction and wear. Chemical reactions between the lubricant additives and surface materials can further enhance the protective effects.
3. Tribochemical reactions: Under high pressure and temperature, the lubricant can undergo chemical reactions with the surface, forming a solid film that reduces friction and wear.
Factors Influencing Boundary Lubrication
Several factors influence the effectiveness of boundary lubrication:
1. Load and pressure: Higher loads and pressures increase the likelihood of direct surface contact, leading to a greater reliance on boundary lubrication.
2. Surface roughness: rougher surfaces provide more contact points, making it challenging to maintain a continuous lubricant film and promoting boundary lubrication.
3. Lubricant properties: The chemical composition and additives of the lubricant play a crucial role in boundary lubrication. Anti-wear and extreme pressure additives enhance the formation of the protective film.
Applications and Examples
Boundary lubrication is commonly encountered in various applications, including:
1. Metal forming processes: When metals are shaped through processes like stamping, drawing, or extrusion, boundary lubrication is essential in reducing friction between the metal and the forming tools.
2. High-pressure gears and bearings: In applications with heavy loads and intermittent high contact pressures, such as gearboxes and heavy machinery, boundary lubrication helps protect the surfaces from excessive wear.
3. Automotive engines: Boundary lubrication occurs in the piston-cylinder interface, where the lubricant film is frequently breached due to elevated temperatures and pressures.
Limitations of Boundary Lubrication
Boundary lubrication offers certain advantages, such as its ability to provide protection under extreme conditions where other regimes may fail. However, it also has limitations:
1. Limited load-bearing capacity: Boundary lubrication cannot support high loads as the lubricant film is thin and easily breached.
2. Increased friction and wear: While boundary lubrication reduces wear compared to dry surfaces, it still exhibits higher friction and wear compared to other lubrication regimes.
3. Sensitivity to operating conditions: Boundary lubrication's effectiveness depends on factors such as temperature, speed, and surface roughness, making it more sensitive to variations in operating conditions.
Understanding boundary lubrication is crucial for selecting appropriate lubricants and additives, optimizing surface finishes, and implementing maintenance strategies to minimize wear and friction.
Mixed Lubrication
The mixed lubrication regime that occurs when both a fluid film layer lubrication and boundary lubrication mechanisms are simultaneously present between two surfaces in relative motion. It serves as a transitional regime between boundary and full-film lubrication. In mixed lubrication, the lubricant film thickness is not sufficient to separate all surfaces, resulting in intermittent contact and partial fluid film formation. Mixed lubrication most commonly occurs at start-up or shutdown.
The characteristics of mixed lubrication include moments of direct contact between the surfaces, as well as partial separation due to the presence of a thin fluid film. Therefore, it has the 2nd highest coefficient of friction amongst the regime types. It combines aspects of both boundary lubrication and full-film lubrication, with the lubricant film thickness being neither fully developed nor completely absent. The lubrication regime can vary along the contacting surfaces, with some regions exhibiting more boundary lubrication and others displaying characteristics of full-film lubrication.
Mixed lubrication relies on a combination of mechanisms to reduce friction and wear. In areas of direct contact, boundary lubrication mechanisms come into play, where additives in the lubricant form a protective film on the surface, minimizing friction and wear. In regions where the lubricant film is thicker, full-film hydrodynamic lubrication mechanisms contribute to load support and reduced friction, although not to the extent of a fully developed fluid film. Does your equipment experience mixed lubrication? Selecting lubricants with the proper additive chemistry protect equipment during these expected periods.
Several factors influence the occurrence and effectiveness of mixed lubrication. Operating conditions, such as moderate speeds and loads, play a role as the fluid film thickness is insufficient for complete separation. Surface roughness also influences the extent of boundary lubrication, with rougher surfaces promoting boundary lubrication in those areas. Additionally, the viscosity, additives, and film-forming characteristics of the lubricant impact the transition between boundary and full-film lubrication within the mixed regime.
Mixed lubrication finds applications in various systems. For example, in automotive engines, the camshaft and lifter interface often experience mixed lubrication due to high contact pressures and the intermittent nature of the motion. Rolling element bearings, specifically the contact between the rolling elements and the raceways, can also exhibit mixed lubrication.
Mixed lubrication offers advantages such as moderate load-carrying capacity due to the combined effect of fluid film and boundary lubrication mechanisms. It also provides improved wear resistance compared to pure boundary lubrication due to the presence of a partial fluid film. However, it has limitations, including increased friction compared to full-film hydrodynamic lubrication due to intermittent contact and sensitivity to operating conditions such as speed, load, and surface roughness.
Caution must be exercised when incorporating additives into lubrication systems, especially in cases where the metallurgy of components involves sensitive materials such as copper-based alloys. While additives can enhance lubrication performance, certain formulations, like sulfur-based extreme pressure additives, can react adversely with these alloys.Top of Form
Understanding mixed lubrication is crucial for optimizing lubricant selection, surface finishes, and operating conditions. By minimizing direct contact and enhancing fluid film formation, the detrimental effects of boundary lubrication can be minimized. In the next section, we will explore full-film hydrodynamic and elastohydrodynamic lubrication (EHL).