Amazing Benefits of Oil Additives
Oil Additives and Their Function in Lubricants
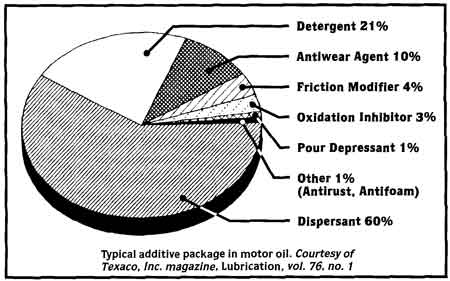
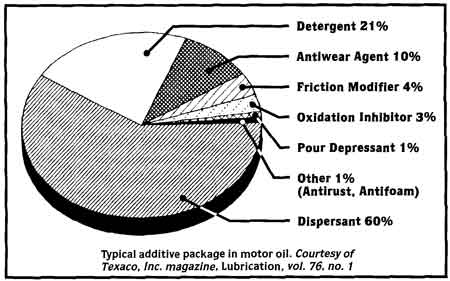
The additives in a lubricant ensure that machinery operates smoothly, with minimal wear and tear to optimize reliability and machine life. Engine oils typically have the highest percentage of additives in a lubricant, reaching up to 30% of its volume. In contrast, phosphate ester hydraulic fluids typically have the lowest percentage of additives or even no additives. Additives perform three general functions:
1. Enhance desirable properties of a lubricant. For example, viscosity index improvers enhance the ability of an oil to maintain its viscosity over a wide range of temperatures.
2. Suppress undesirable properties of a lubricant. For example, antioxidants slow down and suppress future oxidation of an oil which leads to the formation of sludge and deposits.
3. Add a new property to a lubricant. For example, extreme pressure additives add protection against wear under high-pressure conditions.
Whether you are a seasoned engineer, a maintenance professional, or simply curious about the world of industrial lubricants, this blog aims to shed light on the unsung hero of the lubrication world – additives. Join us as we delve deeper into the intricacies of these compounds, their classifications, and their transformative impact on tribology.
Industrial Lubricant Additives
Lubricants are more than just slick agents; they are composed of intricate chemical formulations tailored to specific functions. In the vast world of industrial machinery each moving part may have its own unique needs. Understanding the roles of different additives can be crucial.
Rust & Oxidation (R&O) Inhibitors:
Role: These protect lubricated machinery parts against rust and oxidation. By preventing the oxidation of the oil, they prolong the lifespan of the lubricant and help in maintaining its viscosity over time.
Examples: Sterically hindered phenols and aromatic amines.
Corrosion Inhibitors:
Role: While R&O inhibitors protect the oil, corrosion inhibitors safeguard the machine parts, especially metal components, from corrosive elements present either in the lubricant or the operating environment. Corrosion inhibitors are typically specific to specific metals.
Examples: Tolyltriazole is commonly used in lubricants to protect copper and bronze components from corrosion.
Anti-wear Additives
Role: As the name suggests, these additives are designed to prevent wear in situations where moving parts come into close contact. They form a protective layer on surfaces, preventing direct metal-to-metal contact.
Examples: Zinc dialkyldithiophosphate (ZDDP) is an anti-wear agent typically found in hydraulic oil. ZDDP serves a dual purpose as it also acts as an antioxidant. Tricresyl phosphate (TCP) is a frequently used AW agent, especially in aviation turbine oils.
Extreme Pressure (EP) Additives:
Role: EP additives are for conditions where immense pressure might cause lubricants to break down. They create a protective film on machine parts, ensuring that they do not weld together under high-stress situations.
Examples: Phosphorus-sulfur derivatives, molybdenum disulfide, graphite, sulfurized olefins and dialkyldithiocarbamate complexes.
De-emulsifiers:
Role: These additives help separate water from the oil, ensuring that any moisture that enters the system can be easily removed, thus preventing issues like corrosion or reduced lubrication performance.
Emulsifiers:
Role: Opposite of de-emulsifiers, emulsifiers help oil and water mix, which can be essential in specific applications where water contamination may be unavoidable or metalworking fluids where a stable emulsion can aid in cooling and chip removal.
Friction Modifiers:
Role: Friction modifiers reduce the frictional properties of a lubricant reducing friction as needed, which can be especially important in transmissions or certain types of bearings.
Examples: sulfured compounds, chlorinated compounds and phosphorus-sulfur derivatives
Viscosity Index Improvers:
Role: These additives ensure that a lubricant maintains its viscosity across a broad temperature range, ensuring consistent performance whether in the cold of winter or the heat of summer.
Examples: Polymethacrylates are used to help the oil maintain its viscosity across varying temperatures.
Neutralizers:
Role: Neutralize acidic components that may form during oil degradation or due to external contaminants, ensuring the acidic compounds do not harm the machinery.
Examples: Calcium or magnesium sulfonates and phenates serve as detergent additives, helping to neutralize acidic components and clean internal parts of engines.
Dispersants:
Role: Dispersants keep contaminants suspended in the oil, preventing them from clumping together and forming sludge or varnish, which can impair machine function.
Example: Succinimides, derived from polyisobutylene, help keep contaminants suspended in the oil, preventing sludge formation.
Detergents:
Role: Not to be confused with household detergents, these additives play a role in keeping machinery clean by neutralizing acidic compounds and helping to remove internal deposits.
Examples: Calcium or magnesium sulfonates, calcium or magnesium phenates.
Each of these additives plays a critical role in the formulation of lubricants, ensuring that they perform optimally under various conditions and in various applications. By recognizing the specific chemicals used for each function, professionals can better understand the chemistry behind the lubricants they use and optimize their choices accordingly. In continuation, new trends in oil additive formulation.