Vibration Analysis and Used Oil Analysis Working Together
Vibration Analysis and Used Oil Analysis Working Together
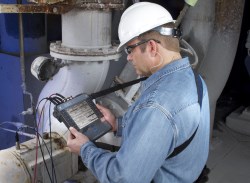
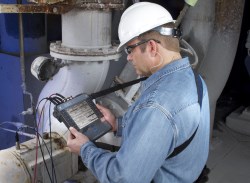
Introduction
Predictive Maintenance is an advanced reliability and maintenance that maximizes machine uptime and reduces unexpected downtime. Predictive maintenance reduces maintenance costs over preventative maintenance since maintenance tasks are performed only when warranted.
Vibration and oil analysis should not be thought of as an “either or” scenario since both have distinct strengths that will enhance your condition monitoring program.
In this blog we will explore how adding or expanding an oil analysis program can enhance overall equipment reliability alongside vibration analysis. Next, we will briefly describe vibration analysis for those who are unfamiliar with the technology.
Understanding Vibration Analysis
Vibration analysis is a cornerstone of predictive maintenance, offering valuable insight into the health of rotating machinery. By measuring and analyzing vibrations, maintenance professionals can detect early signs of mechanical issues, allowing for timely intervention and preventing costly downtime.
At its core, vibration analysis involves monitoring the vibrations produced by rotating machinery. These vibrations are indicative of various mechanical and operational conditions within the equipment. By capturing and analyzing vibration data over time, maintenance teams can identify trends and anomalies that may signal potential problems.
One of the key advantages of vibration analysis is its nonintrusive nature. Unlike some other diagnostic techniques, such as dismantling machinery for inspection, vibration analysis can be performed while the equipment is in operation. This not only saves time and labor but also eliminates the risk of introducing contamination into the machinery.
Vibration frequencies are typically measured in cycles per second, or Hertz (Hz). The frequency spectrum ranges from low to high frequencies, typically spanning from 2 to 10,000 Hz. Low-frequency vibrations are often associated with issues such as misalignment, unbalance, and looseness, while high-frequency vibrations may indicate problems like bearing faults, gear damage, or cavitation.
By understanding the vibration signatures associated with diverse types of machinery and operating conditions, maintenance professionals can effectively diagnose issues and plan appropriate corrective actions. Furthermore, vibration analysis software and tools have become increasingly sophisticated, enabling advanced analytics and predictive modeling to forecast equipment health and anticipate potential failures before they occur.
Exploring Used Oil Analysis
Used oil analysis encompasses a variety of tests and techniques aimed at assessing the physical and chemical properties of lubricating oil, contamination, and wear. Spectroscopic analysis, for instance, involves analyzing the elemental composition of the oil, detecting trace elements that may indicate wear, contamination from external sources and oil additives. Particle counting, on the other hand, quantifies the concentration and size distribution of particles suspended in the oil, helping identify abrasive wear and the presence of contaminants such as dirt or metal fragments.
Additionally, viscosity measurement plays a crucial role in used oil analysis, as changes in viscosity can signify contamination, fluid commingling or degradation of the oil due to thermal or oxidative degradation. Other common tests include acid number, water content wear, contaminant and additive metals, particle counting (ISO code), ferrous wear and acid number. There are many more tests that can provide additional information about the remaining life of the lubricant, type and severity of the wear occurring. These tests are typically when a problem is suspected or on a less frequent basis than the routine tests. Your oil lab can provide insights into what testing may be warranted.
One of the key advantages of used oil analysis is its ability to detect internal wear, contamination, and degradation within your machinery, even before visible (or vibrational) symptoms manifest. By monitoring trends in oil properties over time, maintenance professionals can identify subtle changes indicative of impending issues, allowing for proactive maintenance interventions, and minimizing the risk of catastrophic failures.
Moreover, used oil analysis serves as a valuable tool for assessing the effectiveness of maintenance practices and the performance of lubricants. By tracking parameters such as oxidation levels, additive depletion, and contamination levels, organizations can optimize their lubrication practices, extend equipment life, and reduce overall maintenance costs.