Keeping it Clean – Proactive Strategy to Minimize Lubricant Contamination
Maximize Runtime. Checklist for Minimizing Lubricant Contamination
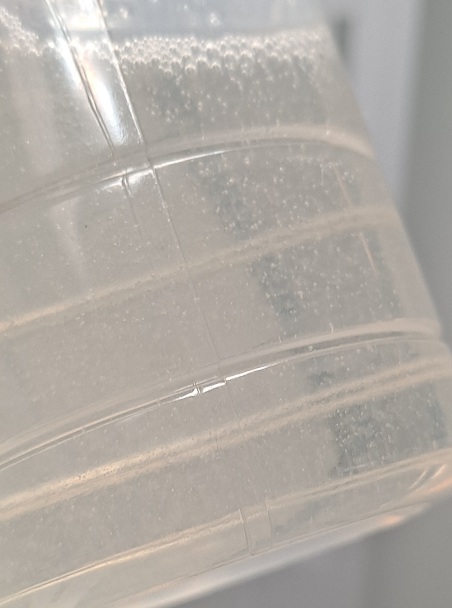
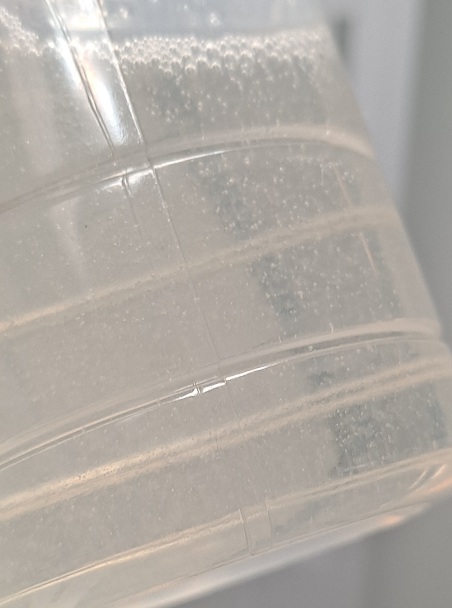
In the world of industrial machinery, clean lubricants are the lifeblood that ensures optimal performance and longevity. Contaminants such as water and dirt are silent enemies, leading to accelerated abrasive wear and corrosion. Industrial process and fuel contamination also pose significant threats to a lubricant’s viscosity and overall lubricating properties, resulting in increased machine downtime and maintenance costs.
Routine oil analysis can detect contaminants, enabling corrective actions to be taken. However, prevention is always better than cure. Preventing contamination before it reaches the machines is a proactive approach that pays dividends in the long run. Studies have shown that preventing contamination is significantly more cost-effective than reacting to an alarm triggered by an oil analysis report. This proactive approach not only saves money but also extends the life of both the lubricants and the machinery they protect. Seventy percent of alarms on oil analysis reports are caused by sample contamination. If left unchecked, contamination accelerates lubricant degradation and increases the wear and corrosion of machine components.
How do we prevent contamination from occurring in the first place? In this blog, we will explore key measures that can be taken to ensure that your lubricants remain clean and effective. By adopting these proactive strategies, you can enhance machine reliability, reduce maintenance costs, and maximize runtime (MRT).
Contamination can be divided into three broad categories: built-in contamination from manufacturing and storage before the machine is put into service, external contamination, and internally generated contamination such as wear particles and lubrication degradation by-products. We will focus on external and internally generated contamination in this blog. Let’s start with proactive strategies to prevent external contamination.
Proactive Strategies
Pre-filtered Oil: The first step to ensuring that a machine is charged with clean oil is using pre-filtered oil. Most oil distributors offer pre-filtered oils and may package the oil into smaller containers. Consult with your lube supplier about the available service options to ensure you receive clean, ready-to-use oil.
Checking New Oil Deliveries: Oil deliveries need to be sampled and sent to the lab to verify cleanliness, check oil quality, and ensure the oil meets the necessary specifications for the application. This crucial step helps address any issues before the oil is used in machinery.
Bulk Tank Inspection: Periodically sample bulk tanks to ensure that the quality of the lubricant remains within cleanliness specifications.
Filter Cart Filtration: Filter carts are essential for keeping the oil clean during transfer from bulk tanks or totes to machines. The oil may need to be transferred from the tote to intermediary containers before reaching the machine. Transferring oil with filter carts ensures it remains uncontaminated. We recommend reading 10 Applications for Filter Carts, by Noria Corporation, for more information on maximizing the use of this important equipment.
Desiccant Breathers Moisture Prevention: Desiccant breathers prevent moisture contamination from entering the lube reservoir. Use a sizing chart to select the correct size breather. Some desiccant breathers are equipped with check valves, extending the life of the desiccant by exposing it to the atmosphere only when necessary. This type of breather is ideal for standby equipment and storage tanks. Service representatives often recommend breathers with check valves for all equipment along the Gulf Coast region due to the high humidity.
Proper Sealing and Ventilation: Ensure that all machinery and storage containers are properly sealed and ventilated to prevent contaminants from entering. Use high-quality seals and gaskets and inspect them regularly for wear and tear.
Routine Maintenance: Implement a routine maintenance schedule that includes regular checks, servicing, and routine analysis of in-service lubricants. This helps in early detection and correction of any potential contamination sources as well as other issues.
Training and Awareness: Educate and train staff on the importance of contamination control, proper handling of lubricants, and best practices for maintaining clean oil. Awareness and adherence to these practices are key to preventing contamination.
By implementing these proactive strategies, you can ensure that your machines are filled with clean oil and that the oil remains clean throughout its use. These measures will help you avoid the pitfalls of contamination, leading to better machine performance, extended lubricant life, and significant cost savings.