Lubricant Contamination Control Check List
Methodical Lubrication Contamination Prevention
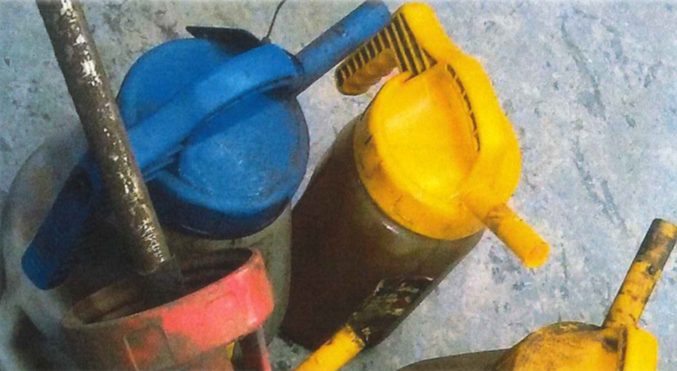
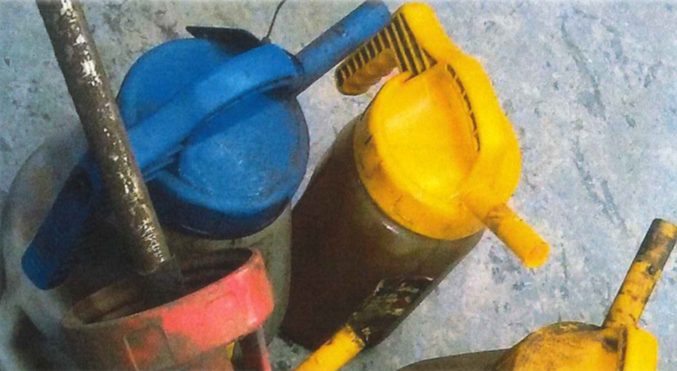
Investing in contamination prevention measures is not just a smart choice—it’s a necessity for any operation aiming to maximize efficiency and longevity. By ensuring that your lubricants remain clean and free from contaminants, you significantly reduce the risk of costly machinery breakdowns and unscheduled downtime. The cost of implementing proactive strategies is a fraction of the expense associated with reactive maintenance and repairs. Consider the long-term benefits: extended equipment life, improved reliability, and sustained productivity. These advantages translate into substantial cost savings and a stronger bottom line. Proactive contamination control measures not only enhance the performance and lifespan of your machinery but also contribute to a safer working environment by minimizing the risk of equipment failure. Budget a portion, or all of these items:
Proper Storage: Store lubricants in a clean, dry environment away from direct sunlight and temperature extremes. Use dedicated storage containers and avoid open containers that can allow contaminants to enter.
Regular Inspection: Conduct regular inspections of lubricant storage areas and machinery. Look for signs of contamination such as changes in oil color, the presence of particles, or unusual odors.
Inspection of Seals and Gaskets: Ensure that all seals and gaskets on machinery and storage containers are in good condition and properly fitted to prevent contaminants from entering.
Clean Transfer Equipment: Always use clean transfer equipment such as pumps, hoses, and containers when moving lubricants. Contaminated equipment can introduce dirt and other particulates into the oil.
Proper Handling Practices: Train personnel in proper handling and dispensing practices. Avoid opening containers unnecessarily, and always clean the area around the fill port before adding oil to machinery.
Condition Monitoring: Implement a condition monitoring program that includes regular sampling and analysis of lubricants. This will help detect any early signs of contamination and allow for timely corrective action.
Filtration Systems: Utilize inline filtration systems to continuously remove contaminants from the oil while it is in use. This can help maintain oil cleanliness and extend the life of both the lubricant and the machinery.
Cleanliness Standards: Establish and enforce cleanliness standards for lubricant storage and handling areas. Implementing a “clean as you go” policy can help prevent contamination from occurring.
Dedicated Tools and Equipment: Use dedicated tools and equipment for different types of lubricants to avoid cross-contamination. For instance, use separate funnels and pumps for synthetic and mineral oils. Cross contamination occurs when one lubricant inadvertently mixes with another. For example, mixing an oil containing a detergent additive with an R&O fluid can destroy the R&O fluid’s water separability. Proper labeling and dedicated containers are essential. One solution is the use of “right-size containers,” which are used once and, if there is unused oil remaining, the oil is disposed of.
Implementing these strategies involves an initial investment in proper equipment, training, and regular maintenance. However, this investment is quickly offset by the reduction in emergency repairs, replacement parts, and labor costs. Choosing to prevent contamination is choosing to protect your investment and ensure the smooth, efficient operation of your machinery. It’s about making a commitment to quality, reliability, and optimal performance. This proactive approach fosters a culture of care and attention to detail that permeates all aspects of your operations, ultimately driving success and profitability.
To take your contamination control strategy to the next level, contact MRT Laboratories. Our team of ICML and STLE certified professionals can assist you in establishing or improving your current oil analysis program, selecting the right tests, and determining the appropriate testing frequencies. Together, we can enhance your machinery’s performance, extend its lifespan, and significantly reduce your maintenance costs.