Understanding Machine Wear and Failure Mechanisms
Equipment wear can be categorized to thoughtfully apply the appropriate maintenance application
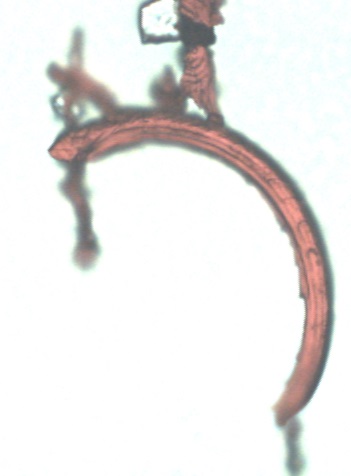
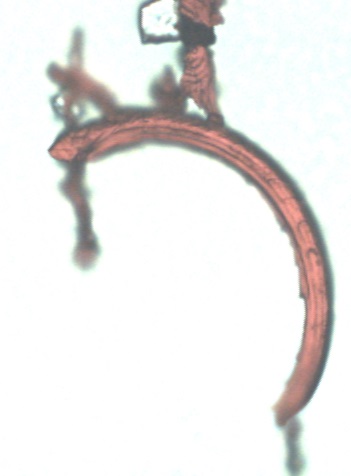
For maintenance and reliability professionals, a deep understanding of machine wear and its underlying causes is essential for making pre-emptive informed decisions. Recognizing whether wear is driven by mechanical stress, contamination, or lubricant breakdown enables engineers and technicians to identify issues early, and before they escalate into major failures. Oil analysis plays a crucial role in this process by providing detailed insights into both lubricant and machinery conditions, supporting a proactive maintenance approach that significantly reduces downtime and extends equipment life.
Causes of Wear in Machines
Mechanical Stress
Mechanical stress is the primary driver of machine wear. Continuous cyclic loads, vibration, or shock can induce microstructural changes that eventually lead to fatigue, causing small cracks or even complete material failure. Whether stemming from misalignment, overloading, or regular operation, understanding these stress factors allows engineers to design components that are more resilient to such forces.
Contamination
Contaminants may be classified as solid, liquid, or gas. Common solid contaminants include dirt and metal shavings, while water is a frequent liquid contaminant, and process gases often represent gaseous contaminants, particularly in compressor systems. When these particles enter a machine’s lubricating system, they can act as abrasives—scratching and wearing down surfaces. Additionally, liquid and gas contaminants can alter lubricant viscosity, reducing fluid film thickness and increasing friction. This can lead to accelerated wear and even corrosion, which degrades machine components and shortens their service life. Stringent filtration and regular maintenance are essential to mitigating these risks.
Lubricant Breakdown
Lubricants reduce friction and dissipate heat between moving parts, but over time they can degrade due to oxidation, thermal stress, or contamination. As the lubricant’s protective properties diminish, equipment friction increases which accelerates wear and increases mechanical stress. Monitoring you in-service lubricant’s condition through scheduled oil analysis ensures that any degradation is identified early, preventing further damage.
Common Wear Mechanisms
Abrasive Wear (Two-Body and Three-Body)
- Two-Body Abrasion Wear Mechanism
Two surfaces slide directly against each other without intermediary particles. Inadequate lubrication, whether a result of low oil viscosity, an insufficient lubricant film, high contact stresses, misalignment, or rough surface finishes, can cause two-body abrasion. Preventative measures include (1) using the correct lubricant at the proper viscosity, (2) maintaining precise alignment, and (3) ensuring high-quality surface finishes. Regular oil analysis can detect early wear signs and confirming whether the lubrication system is performing optimally.
- Three-Body Abrasion Wear Mechanism
When loose particles such as dust, dirt, or wear debris become trapped between sliding surfaces, they act as a third body that intensifies abrasive effects. Proper filtration, maintaining a clean operating environment, and deliberately productive lubrication practices are critical in preventing three-body abrasion. Routine oil analysis can detect elevated particulate levels, allowing maintenance teams to intervene before significant damage occurs.
Surface Fatigue (Contact Fatigue)
Surface fatigue develops from repeated cyclic stresses that initiate micro-cracks on a material’s surface, leading to material loss and spalling. High contact stress from heavy loads, increased vibration, shock loads, and elevated temperatures all accelerate this process. Inadequate lubrication, misalignment, and contaminants further contribute to uneven load distribution and friction. Regular oil analysis helps detect fatigue early so that maintenance can be performed before severe failures develop.
Adhesive Wear
Adhesive wear is commonly observed in components subjected to frequent metal-to-metal contact under high pressures and sliding conditions, such as gear teeth and sliding surfaces. Under high pressure, microscopic asperities on contacting surfaces may fuse and then break apart as the surfaces slide, removing small material fragments. If the oil viscosity is too low for the required application, the lubricant may not maintain an adequate protective film, increasing the risk of adhesive wear. Maintaining the recommended optimal viscosity and if needed, the use of extreme pressure (EP) additives help sustain a robust lubricating film. Oil analysis measures viscosity and EP additive levels, ensuring the right oil is in use and detecting degradation before significant damage occurs.
Corrosive Wear
Corrosive wear occurs due to chemical or electrochemical reactions between machinery materials and their environment, leading to surface degradation. Prolonged exposure to moisture, acidic or alkaline contaminants, high temperatures, or corrosive chemicals can accelerate this process. Additionally, the breakdown of oil additives and protective coatings reduces the oil's ability to neutralize harmful substances. Preventative measures include using oils with robust corrosion inhibitors, controlling exposure to corrosive elements, and maintaining regular cleaning and maintenance routines. Regular oil analysis monitors chemical properties and additive levels, allowing early detection and intervention.
Cavitation Wear
Cavitation wear occurs when vapor bubbles form within a lubricant and collapse rapidly near a surface, creating shockwaves that erode the material. Factors that contribute to cavitation include high fluid velocities, rapid pressure fluctuations, elevated temperatures, and inadequate lubrication. In pump systems, insufficient fluid input or leaks can create low-pressure zones that promote bubble formation. Preventive measures include using oils designed to resist cavitation, ensuring a stable fluid supply, and optimizing system design to avoid pressure drops. Regular oil analysis identifies early changes in oil properties that may indicate the onset of cavitation.